汽车车轮的设计要求有哪些?在进行汽车车轮设计过程当中,我们需要制作哪些实验?这些实验需要满足哪些要求?所有的这一切都是我们进行车轮设计的核心的关键环节。大家好,我是汽车设计工匠。我们今天接着之前的课程来讲解汽车车轮的相关知识。
01、车轮密封性
将试验用未经过涂装的车轮的气门嘴孔密封,车轮的两侧面用带有密封垫的压板压紧,使其密封,再将整个车轮浸入盛满水的水箱内。试验时,充入的压缩空气压力应≥400kPa,充气达到规定气压后30s内,车轮轮辋任何部位不能有任何气泡逸出。
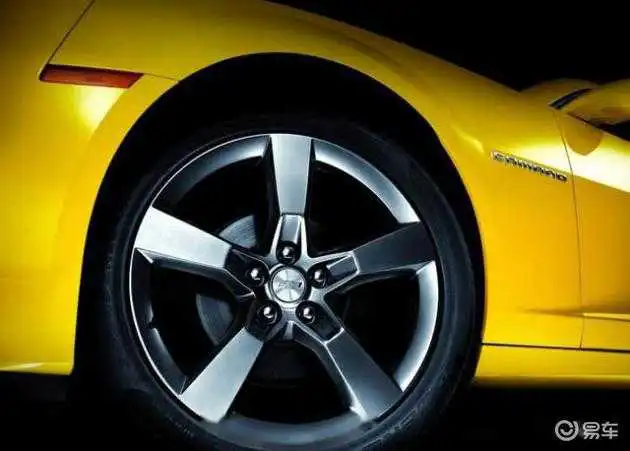
02、车轮的冲击试验
试验环境温度为10℃~38℃,试验设备按GB/T15704-1995中的相应条款规定进行,试验用的轮胎选用整车规定的与之匹配的轮胎,试验方法按GB/T15704中的相应条款规定进行。
试验完后,出现下列情况之一即判定为损坏:轮辐的任一断面处有目测可见的穿透裂纹;轮辐从轮辋上分离;轮胎气压在一分钟内漏尽。
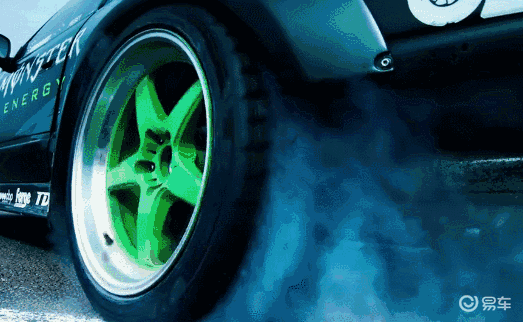
具体试验如下:
a. 轮胎的充气压力必须按车辆制造厂的规定,如无此规定,可按 200kPa充气。
b. 冲头质量为D,确定公式:D=0.6W/180。
式中: D—冲头质量 ±2%;W—最大车轮静载荷,kg
c. 把试验车轮轮胎总成安装在与车辆轮毂一致的连接盘上。车轮安装时,要按车辆或车轮制造厂推荐的方法或用手工拧紧至规定值。
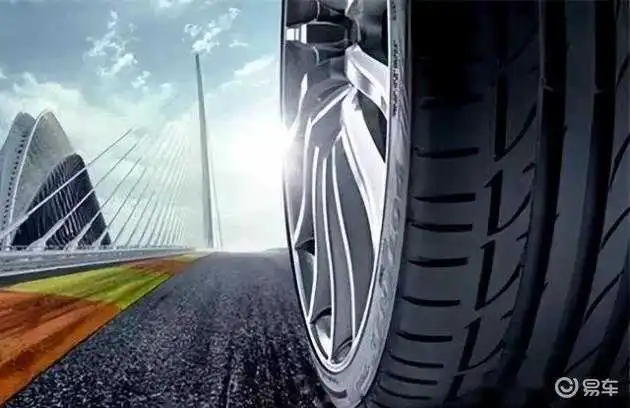
d. 调整冲头下落高度,冲头的下落高度应在轮辋轮缘的最高点上方230±2mm。
e. 调整冲头对车轮的冲击位置,冲头置于轮胎上方,其带有圆角的冲击面刃缘应与轮辋轮缘重叠 25±1mm。
f. 利用试验设备的快速释放机构,让冲头落下,冲击车轮轮胎总成。
03、轮胎尺寸要求
根据整车规定初步选定所需车轮的规格尺寸(主要是轮辋轮辐的参数)和轮胎的规格,此时应综合考虑车轮、轮胎的供应商和GB/T2978《轿车轮胎系列》来设计匹配,选择轮胎时还应考虑到轮胎的负荷指数、侧偏刚度、速度级别以及胎面花纹,以及轮胎的3c认证及美国的DOT认证等。同时,必须考虑所开发或选用的车轮和轮胎之间的匹配性。
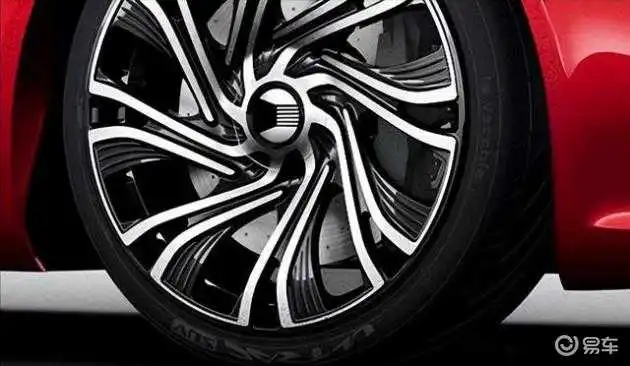
04、轮胎强度
试验室温度应保持在18℃~36℃;其他试验条件、试验方法按照GB/T4053-1996中相应规定执行,试验后轮胎的强度试验破坏能应不低于下表中规定。
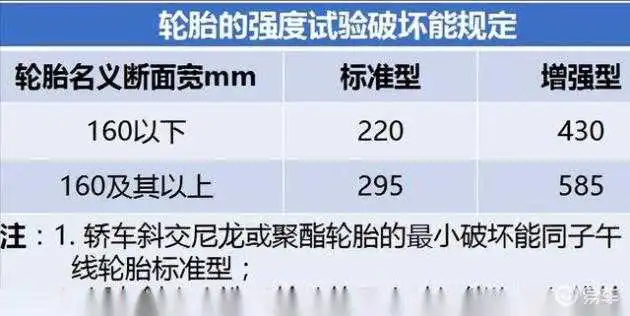
具体试验如下:
a. 将试验轮胎充入规定气压,在试验室温度下至少停放3h后,再重新调到规定气压。
b. 将轮胎固定在试验机上,沿轮胎胎面中心线取大致间隔相等的5个点进行试验。
c. 压头垂直于胎面,并压在靠近胎面圆周中心线的花纹块上,避免压入花纹沟中。
d. 测量每个点的轮胎破坏前瞬时的压力和压入探度(行程),或压头触及轮辆的瞬时压力和行程。在转入下一个点试验前校正气压。

e. 采用自动计算破坏能装置时,当达到规定的最小破坏能后,立即停止压头继续压入轮胎。
f. 如果压头触及轮辋,轮胎未压穿,且未达到最小破坏能值,则此点视为达到最小破坏能。
试验过程中,如果无内胎轮胎无法保持充气压力,允许装入内胎。
g. 计算各点的破坏能:W=F*P/2000。
注:F表示作用力N,P表示行程mm
h. 计算出各点的破坏能的算术平均值,作为该轮胎的破坏能。
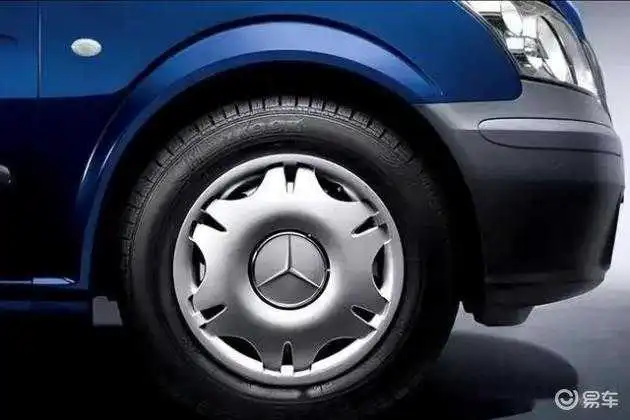
05、脱圈阻力(检查轮胎和轮辋结合紧密程度)
轮胎经GB/T4504(ISO10191:1993)中规定的试验条件和试验方法进行轮胎脱圈阻力试验,每点的脱圈阻力值应不低于下表相应的规定值。
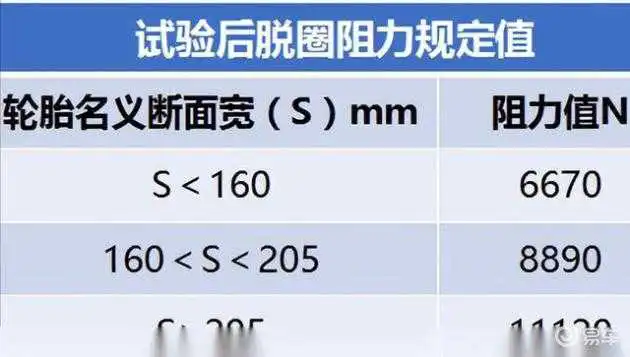
具体试验如下:
a. 将轮胎轮组合体在18℃-36℃的温度下至少停放3h后,再重新调到规定气压。
b. 将轮胎轮辋组合体安装在脱圈阻力试验机上,按规定距离调整脱圈压块的位置。
c. 在轮胎胎侧圆周面上确定至少4 个等间隔点,逐点进行试验。
d. 脱圈压块以规定的下降速度,向胎侧外表面施加压力,直到轮胎与轮辋脱开或达到下表规定的最小脱圈阻力值时为止。记录脱圈时或停止试验时的阻力值。
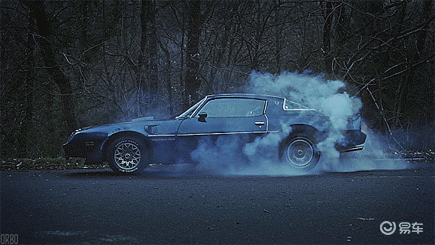
06、高速性能(转鼓法)
轮胎安装在符合规定的标准轮辋上,按下表中规定的气压充气;试验室温度应保持在38℃±3℃。按GB/T7034(ISO10191:1993)进行试验后,轮胎气压不应低于规定的初始气压;轮胎外观检查不应有(胎面、胎侧、帘布层、气密层、带束层、胎圈)脱层,帘布层裂缝、帘线剥离、帘线断裂、崩花、接头裂开、龟裂等缺陷。
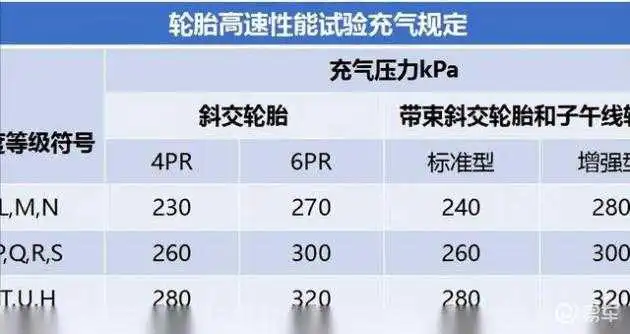
具体试验如下:
a. 将轮胎轮辋组合体在38C士3℃的温度下至少停放3h。
b. 转鼓以匀加速启动到初始试验速度的时间应在10min以内。
c. 其他试验阶段改变速度到速度稳定,所需时间小于1min。
d. 将停放后的轮胎气压重新调整到规定值,再停放15min后,测量轮胎主要尺寸。
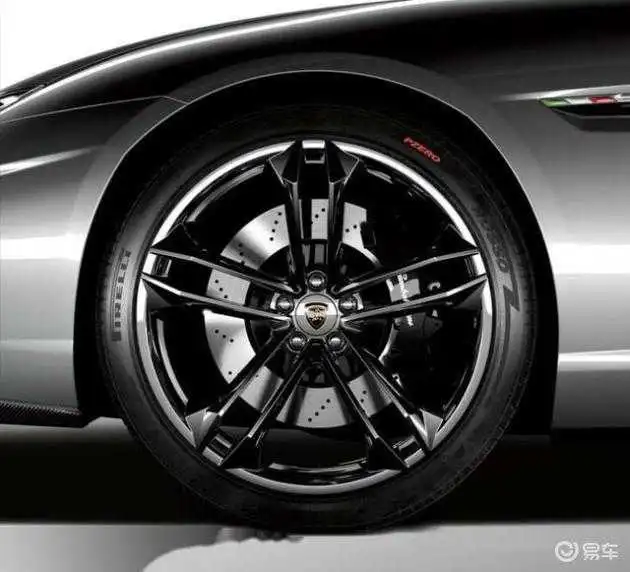
e. 将按上述条件准备好的轮胎轮辋组合体安装在试验轴上,使之垂直转鼓外表面加压,并按规定条件进行试验。
f. 试验按规定程序连续进行,其间不得中断,不得重新调整气压,试验负荷必须保持不变。
g. 轮胎按规定程序完成试验后,要立即停机测量轮胎的气压和主要尺寸,待自然冷却1h后,放掉气压,卸下轮胎进行外观检查。
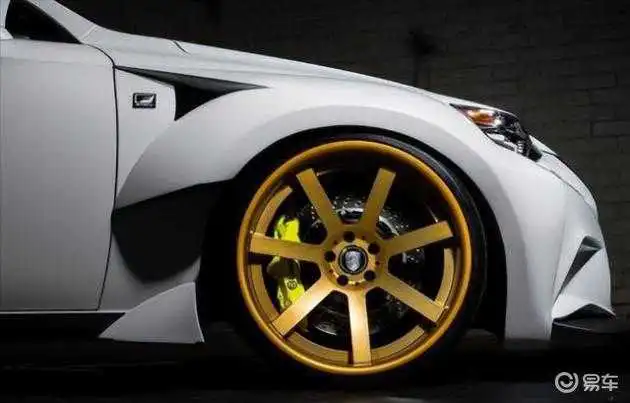
07、耐久性能(转鼓法检查轮胎高负荷连续运行能力)
轮胎安装在符合规定的标准轮辋上,充以下表中规定的气压,将轮胎轮辋组合体在38℃士3℃的温度下至少停放3h。轮胎按GB/T4502(ISO10191:1993)规定的试验条件和试验方法进行耐久性试验后,轮胎气压不应低于规定的初始气压,轮胎外观检查不应有(胎面、胎侧、帘布层等)脱层、帘布层裂缝、帘线剥离、泵花、接头裂开、龟裂等缺陷。具体试验类似上述高速性能测试。
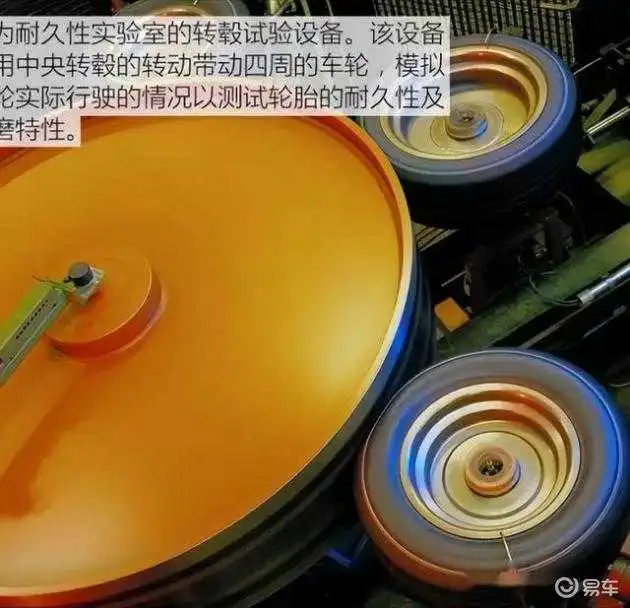
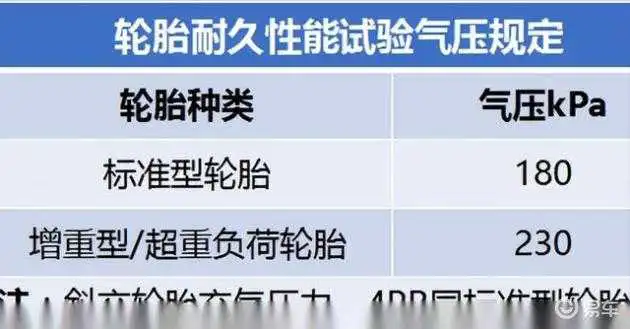
08、车轮整车匹配试验
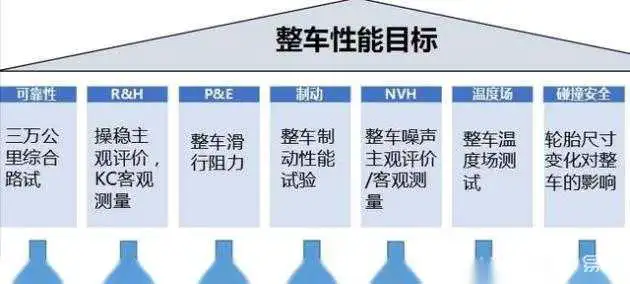
你还知道哪些汽车车轮的相关的知识,欢迎在评论区留言,我是汽车设计工匠,我们下期再聊。
汽车车轮的设计要求有哪些?在进行汽车车轮设计过程当中,我们需要制作哪些实验?这些实验需要满足哪些要求?所有的这一切都是我们进行车轮设计的核心的关键环节。大家好,我是汽车设计工匠。我们今天接着之前的课程来讲解汽车车轮的相关知识。
01、车轮密封性
将试验用未经过涂装的车轮的气门嘴孔密封,车轮的两侧面用带有密封垫的压板压紧,使其密封,再将整个车轮浸入盛满水的水箱内。试验时,充入的压缩空气压力应≥400kPa,充气达到规定气压后30s内,车轮轮辋任何部位不能有任何气泡逸出。
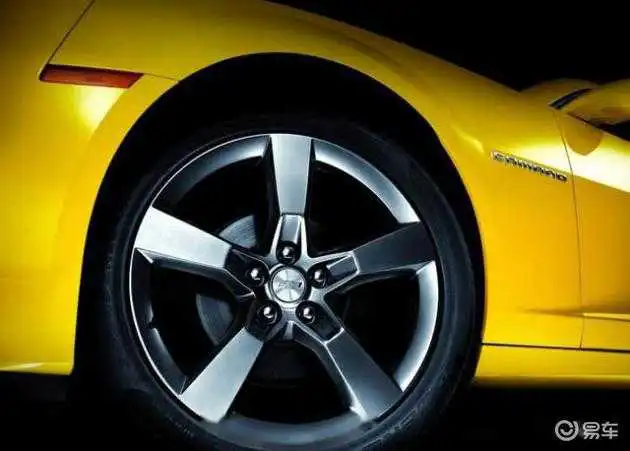
02、车轮的冲击试验
试验环境温度为10℃~38℃,试验设备按GB/T15704-1995中的相应条款规定进行,试验用的轮胎选用整车规定的与之匹配的轮胎,试验方法按GB/T15704中的相应条款规定进行。
试验完后,出现下列情况之一即判定为损坏:轮辐的任一断面处有目测可见的穿透裂纹;轮辐从轮辋上分离;轮胎气压在一分钟内漏尽。
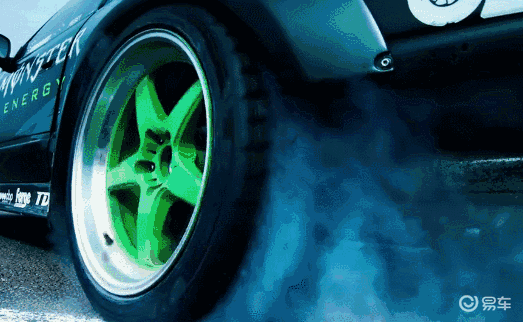
具体试验如下:
a. 轮胎的充气压力必须按车辆制造厂的规定,如无此规定,可按 200kPa充气。
b. 冲头质量为D,确定公式:D=0.6W/180。
式中: D—冲头质量 ±2%;W—最大车轮静载荷,kg
c. 把试验车轮轮胎总成安装在与车辆轮毂一致的连接盘上。车轮安装时,要按车辆或车轮制造厂推荐的方法或用手工拧紧至规定值。
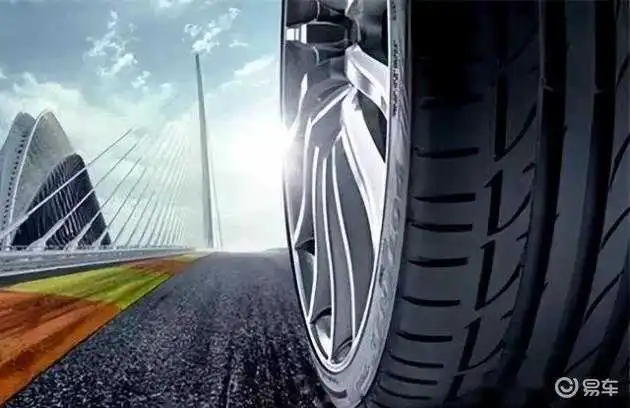
d. 调整冲头下落高度,冲头的下落高度应在轮辋轮缘的最高点上方230±2mm。
e. 调整冲头对车轮的冲击位置,冲头置于轮胎上方,其带有圆角的冲击面刃缘应与轮辋轮缘重叠 25±1mm。
f. 利用试验设备的快速释放机构,让冲头落下,冲击车轮轮胎总成。
03、轮胎尺寸要求
根据整车规定初步选定所需车轮的规格尺寸(主要是轮辋轮辐的参数)和轮胎的规格,此时应综合考虑车轮、轮胎的供应商和GB/T2978《轿车轮胎系列》来设计匹配,选择轮胎时还应考虑到轮胎的负荷指数、侧偏刚度、速度级别以及胎面花纹,以及轮胎的3c认证及美国的DOT认证等。同时,必须考虑所开发或选用的车轮和轮胎之间的匹配性。
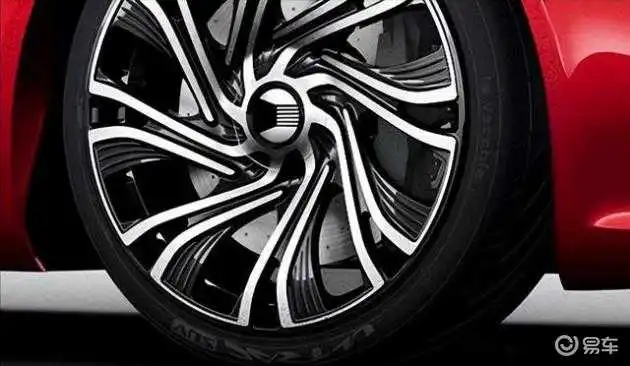
04、轮胎强度
试验室温度应保持在18℃~36℃;其他试验条件、试验方法按照GB/T4053-1996中相应规定执行,试验后轮胎的强度试验破坏能应不低于下表中规定。
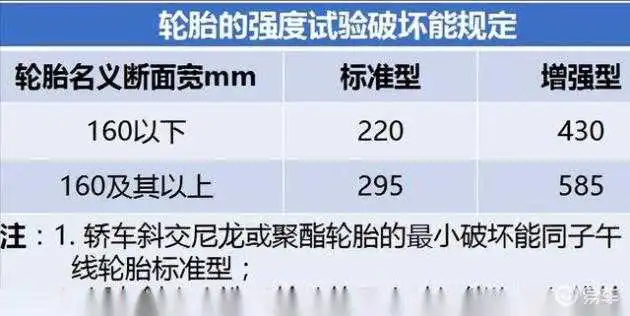
具体试验如下:
a. 将试验轮胎充入规定气压,在试验室温度下至少停放3h后,再重新调到规定气压。
b. 将轮胎固定在试验机上,沿轮胎胎面中心线取大致间隔相等的5个点进行试验。
c. 压头垂直于胎面,并压在靠近胎面圆周中心线的花纹块上,避免压入花纹沟中。
d. 测量每个点的轮胎破坏前瞬时的压力和压入探度(行程),或压头触及轮辆的瞬时压力和行程。在转入下一个点试验前校正气压。

e. 采用自动计算破坏能装置时,当达到规定的最小破坏能后,立即停止压头继续压入轮胎。
f. 如果压头触及轮辋,轮胎未压穿,且未达到最小破坏能值,则此点视为达到最小破坏能。
试验过程中,如果无内胎轮胎无法保持充气压力,允许装入内胎。
g. 计算各点的破坏能:W=F*P/2000。
注:F表示作用力N,P表示行程mm
h. 计算出各点的破坏能的算术平均值,作为该轮胎的破坏能。
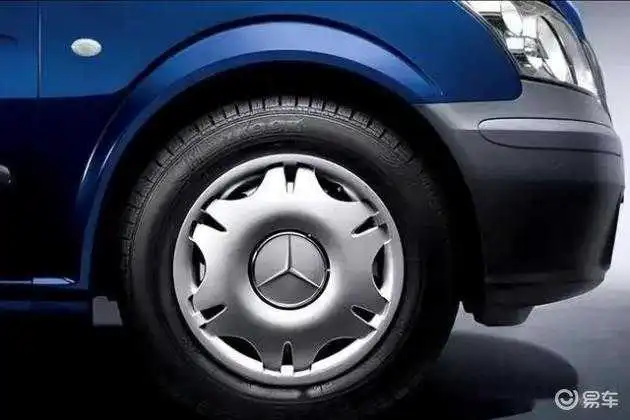
05、脱圈阻力(检查轮胎和轮辋结合紧密程度)
轮胎经GB/T4504(ISO10191:1993)中规定的试验条件和试验方法进行轮胎脱圈阻力试验,每点的脱圈阻力值应不低于下表相应的规定值。
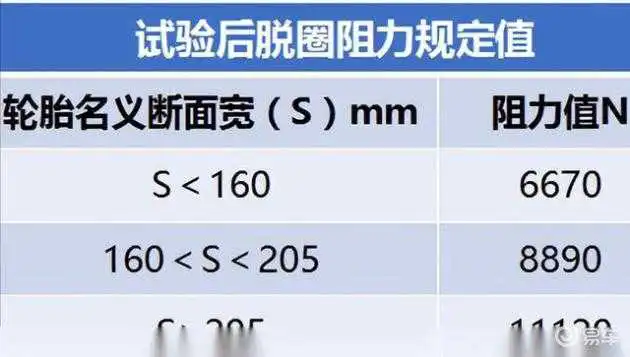
具体试验如下:
a. 将轮胎轮组合体在18℃-36℃的温度下至少停放3h后,再重新调到规定气压。
b. 将轮胎轮辋组合体安装在脱圈阻力试验机上,按规定距离调整脱圈压块的位置。
c. 在轮胎胎侧圆周面上确定至少4 个等间隔点,逐点进行试验。
d. 脱圈压块以规定的下降速度,向胎侧外表面施加压力,直到轮胎与轮辋脱开或达到下表规定的最小脱圈阻力值时为止。记录脱圈时或停止试验时的阻力值。
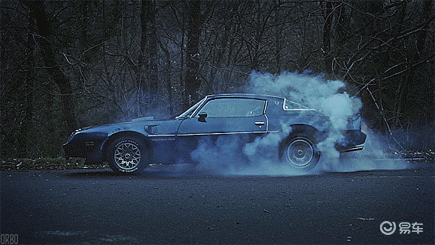
06、高速性能(转鼓法)
轮胎安装在符合规定的标准轮辋上,按下表中规定的气压充气;试验室温度应保持在38℃±3℃。按GB/T7034(ISO10191:1993)进行试验后,轮胎气压不应低于规定的初始气压;轮胎外观检查不应有(胎面、胎侧、帘布层、气密层、带束层、胎圈)脱层,帘布层裂缝、帘线剥离、帘线断裂、崩花、接头裂开、龟裂等缺陷。
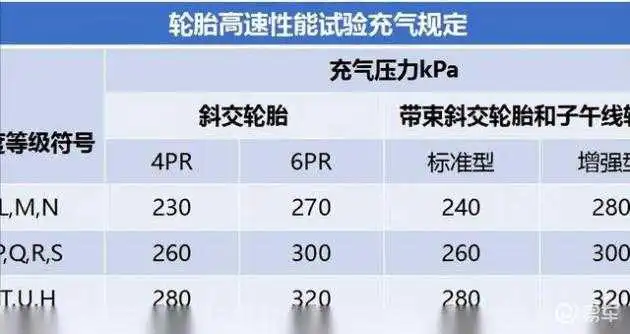
具体试验如下:
a. 将轮胎轮辋组合体在38C士3℃的温度下至少停放3h。
b. 转鼓以匀加速启动到初始试验速度的时间应在10min以内。
c. 其他试验阶段改变速度到速度稳定,所需时间小于1min。
d. 将停放后的轮胎气压重新调整到规定值,再停放15min后,测量轮胎主要尺寸。
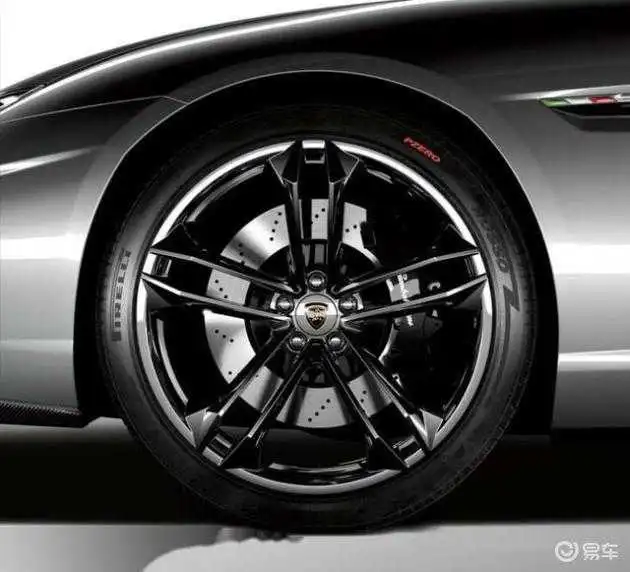
e. 将按上述条件准备好的轮胎轮辋组合体安装在试验轴上,使之垂直转鼓外表面加压,并按规定条件进行试验。
f. 试验按规定程序连续进行,其间不得中断,不得重新调整气压,试验负荷必须保持不变。
g. 轮胎按规定程序完成试验后,要立即停机测量轮胎的气压和主要尺寸,待自然冷却1h后,放掉气压,卸下轮胎进行外观检查。
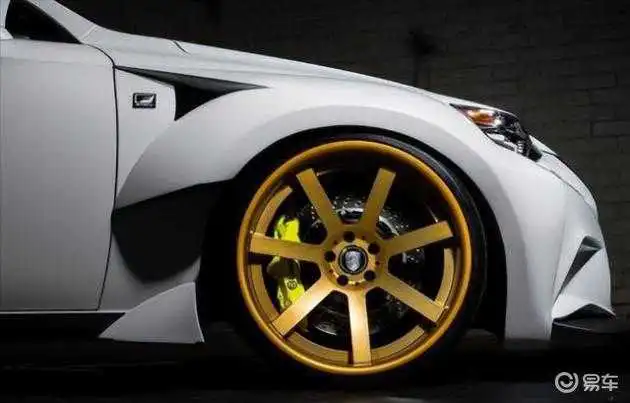
07、耐久性能(转鼓法检查轮胎高负荷连续运行能力)
轮胎安装在符合规定的标准轮辋上,充以下表中规定的气压,将轮胎轮辋组合体在38℃士3℃的温度下至少停放3h。轮胎按GB/T4502(ISO10191:1993)规定的试验条件和试验方法进行耐久性试验后,轮胎气压不应低于规定的初始气压,轮胎外观检查不应有(胎面、胎侧、帘布层等)脱层、帘布层裂缝、帘线剥离、泵花、接头裂开、龟裂等缺陷。具体试验类似上述高速性能测试。
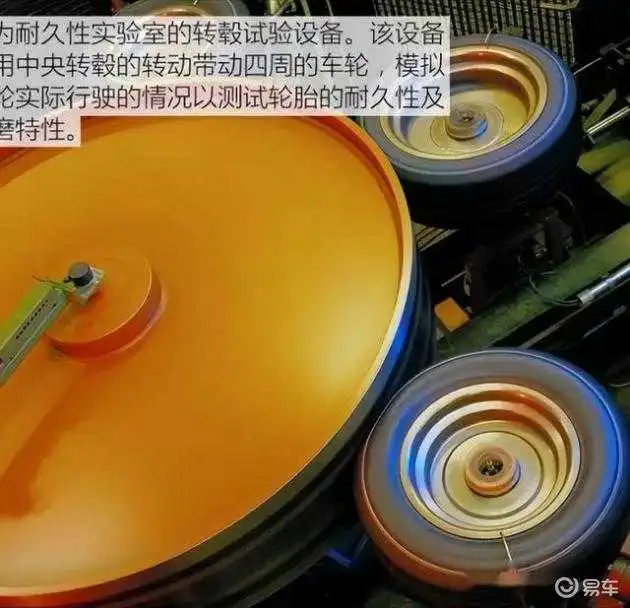
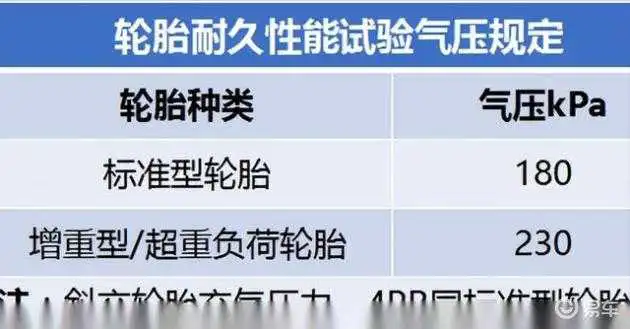
08、车轮整车匹配试验
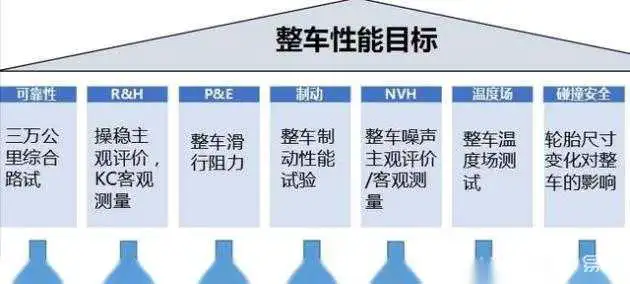
你还知道哪些汽车车轮的相关的知识,欢迎在评论区留言,我是汽车设计工匠,我们下期再聊。
汽车车轮的设计要求有哪些?在进行汽车车轮设计过程当中,我们需要制作哪些实验?这些实验需要满足哪些要求?所有的这一切都是我们进行车轮设计的核心的关键环节。大家好,我是汽车设计工匠。我们今天接着之前的课程来讲解汽车车轮的相关知识。
01、车轮密封性
将试验用未经过涂装的车轮的气门嘴孔密封,车轮的两侧面用带有密封垫的压板压紧,使其密封,再将整个车轮浸入盛满水的水箱内。试验时,充入的压缩空气压力应≥400kPa,充气达到规定气压后30s内,车轮轮辋任何部位不能有任何气泡逸出。
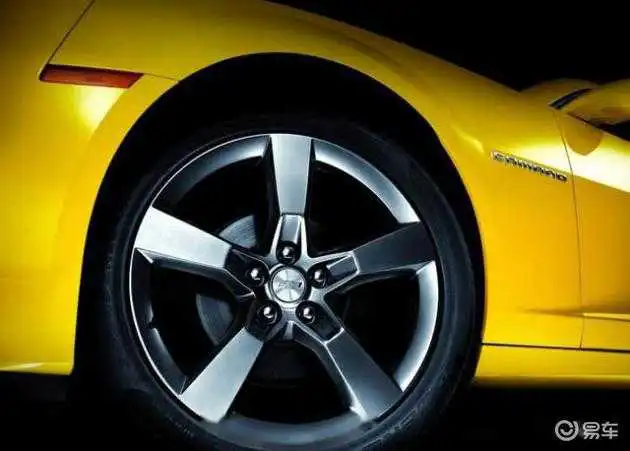
02、车轮的冲击试验
试验环境温度为10℃~38℃,试验设备按GB/T15704-1995中的相应条款规定进行,试验用的轮胎选用整车规定的与之匹配的轮胎,试验方法按GB/T15704中的相应条款规定进行。
试验完后,出现下列情况之一即判定为损坏:轮辐的任一断面处有目测可见的穿透裂纹;轮辐从轮辋上分离;轮胎气压在一分钟内漏尽。
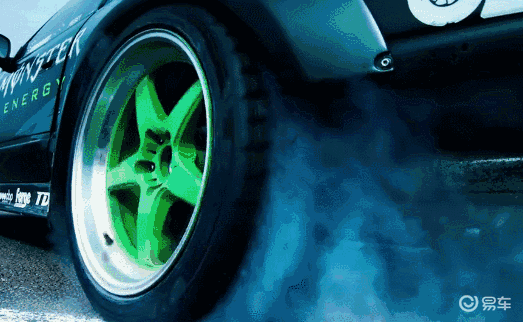
具体试验如下:
a. 轮胎的充气压力必须按车辆制造厂的规定,如无此规定,可按 200kPa充气。
b. 冲头质量为D,确定公式:D=0.6W/180。
式中: D—冲头质量 ±2%;W—最大车轮静载荷,kg
c. 把试验车轮轮胎总成安装在与车辆轮毂一致的连接盘上。车轮安装时,要按车辆或车轮制造厂推荐的方法或用手工拧紧至规定值。
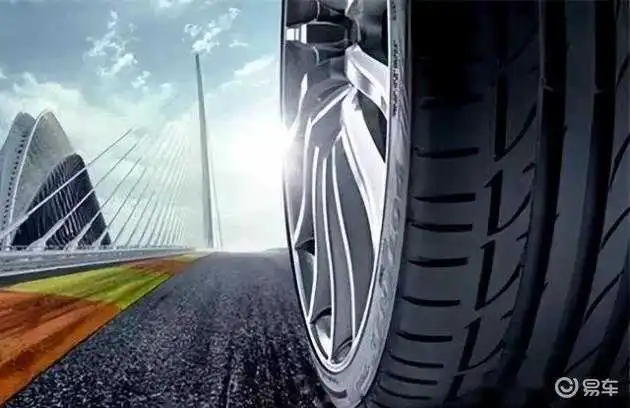
d. 调整冲头下落高度,冲头的下落高度应在轮辋轮缘的最高点上方230±2mm。
e. 调整冲头对车轮的冲击位置,冲头置于轮胎上方,其带有圆角的冲击面刃缘应与轮辋轮缘重叠 25±1mm。
f. 利用试验设备的快速释放机构,让冲头落下,冲击车轮轮胎总成。
03、轮胎尺寸要求
根据整车规定初步选定所需车轮的规格尺寸(主要是轮辋轮辐的参数)和轮胎的规格,此时应综合考虑车轮、轮胎的供应商和GB/T2978《轿车轮胎系列》来设计匹配,选择轮胎时还应考虑到轮胎的负荷指数、侧偏刚度、速度级别以及胎面花纹,以及轮胎的3c认证及美国的DOT认证等。同时,必须考虑所开发或选用的车轮和轮胎之间的匹配性。
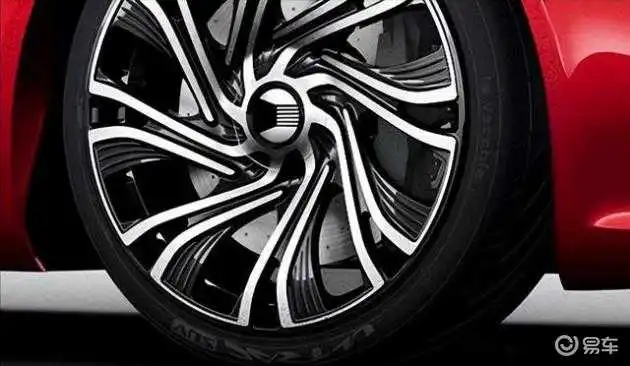
04、轮胎强度
试验室温度应保持在18℃~36℃;其他试验条件、试验方法按照GB/T4053-1996中相应规定执行,试验后轮胎的强度试验破坏能应不低于下表中规定。
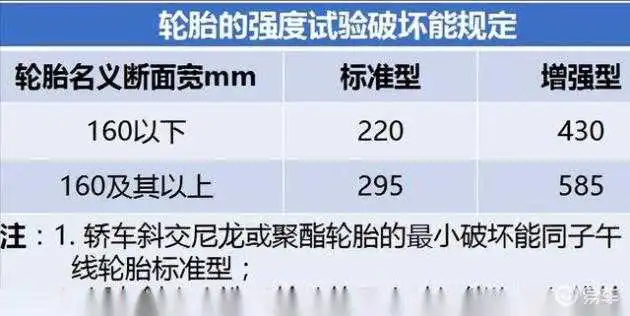
具体试验如下:
a. 将试验轮胎充入规定气压,在试验室温度下至少停放3h后,再重新调到规定气压。
b. 将轮胎固定在试验机上,沿轮胎胎面中心线取大致间隔相等的5个点进行试验。
c. 压头垂直于胎面,并压在靠近胎面圆周中心线的花纹块上,避免压入花纹沟中。
d. 测量每个点的轮胎破坏前瞬时的压力和压入探度(行程),或压头触及轮辆的瞬时压力和行程。在转入下一个点试验前校正气压。

e. 采用自动计算破坏能装置时,当达到规定的最小破坏能后,立即停止压头继续压入轮胎。
f. 如果压头触及轮辋,轮胎未压穿,且未达到最小破坏能值,则此点视为达到最小破坏能。
试验过程中,如果无内胎轮胎无法保持充气压力,允许装入内胎。
g. 计算各点的破坏能:W=F*P/2000。
注:F表示作用力N,P表示行程mm
h. 计算出各点的破坏能的算术平均值,作为该轮胎的破坏能。
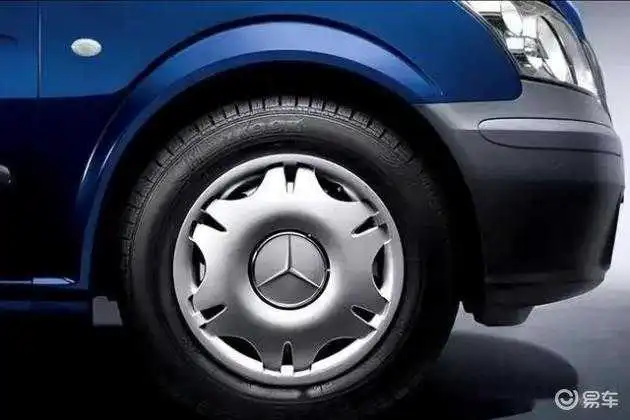
05、脱圈阻力(检查轮胎和轮辋结合紧密程度)
轮胎经GB/T4504(ISO10191:1993)中规定的试验条件和试验方法进行轮胎脱圈阻力试验,每点的脱圈阻力值应不低于下表相应的规定值。
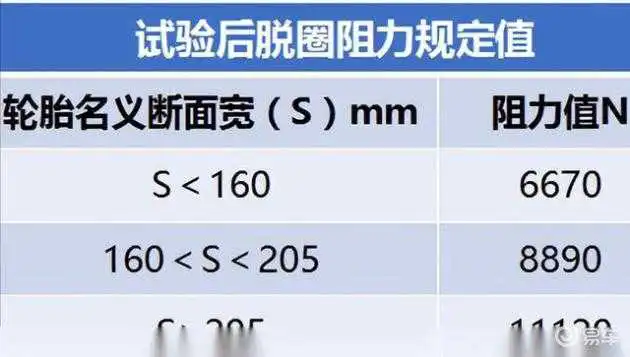
具体试验如下:
a. 将轮胎轮组合体在18℃-36℃的温度下至少停放3h后,再重新调到规定气压。
b. 将轮胎轮辋组合体安装在脱圈阻力试验机上,按规定距离调整脱圈压块的位置。
c. 在轮胎胎侧圆周面上确定至少4 个等间隔点,逐点进行试验。
d. 脱圈压块以规定的下降速度,向胎侧外表面施加压力,直到轮胎与轮辋脱开或达到下表规定的最小脱圈阻力值时为止。记录脱圈时或停止试验时的阻力值。
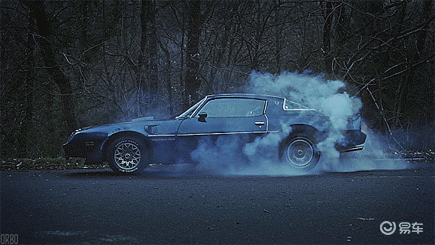
06、高速性能(转鼓法)
轮胎安装在符合规定的标准轮辋上,按下表中规定的气压充气;试验室温度应保持在38℃±3℃。按GB/T7034(ISO10191:1993)进行试验后,轮胎气压不应低于规定的初始气压;轮胎外观检查不应有(胎面、胎侧、帘布层、气密层、带束层、胎圈)脱层,帘布层裂缝、帘线剥离、帘线断裂、崩花、接头裂开、龟裂等缺陷。
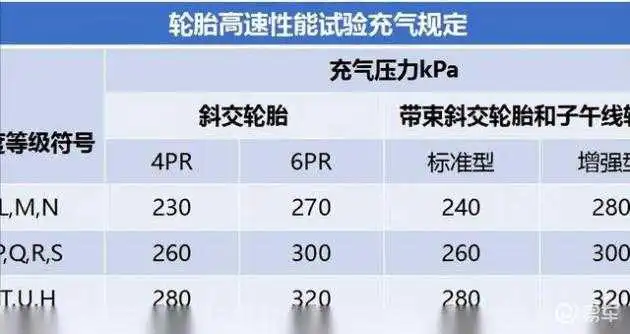
具体试验如下:
a. 将轮胎轮辋组合体在38C士3℃的温度下至少停放3h。
b. 转鼓以匀加速启动到初始试验速度的时间应在10min以内。
c. 其他试验阶段改变速度到速度稳定,所需时间小于1min。
d. 将停放后的轮胎气压重新调整到规定值,再停放15min后,测量轮胎主要尺寸。
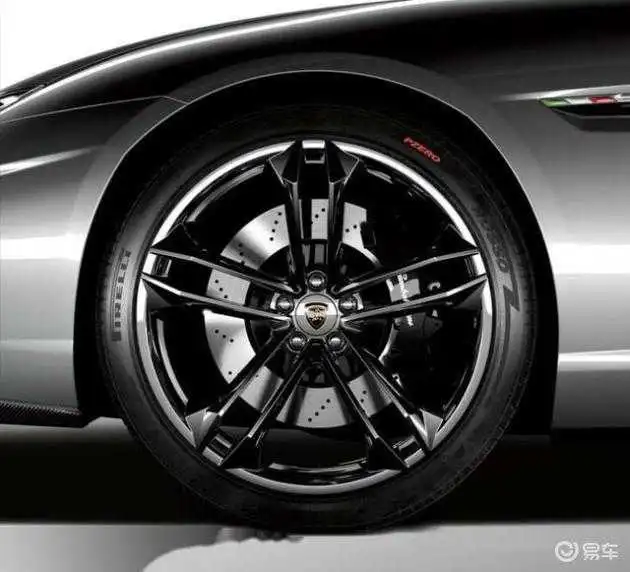
e. 将按上述条件准备好的轮胎轮辋组合体安装在试验轴上,使之垂直转鼓外表面加压,并按规定条件进行试验。
f. 试验按规定程序连续进行,其间不得中断,不得重新调整气压,试验负荷必须保持不变。
g. 轮胎按规定程序完成试验后,要立即停机测量轮胎的气压和主要尺寸,待自然冷却1h后,放掉气压,卸下轮胎进行外观检查。
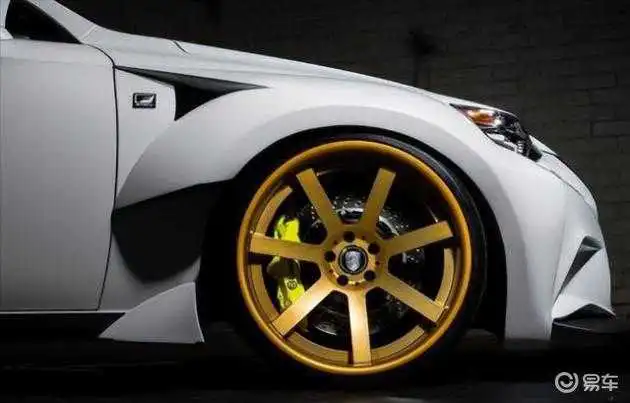
07、耐久性能(转鼓法检查轮胎高负荷连续运行能力)
轮胎安装在符合规定的标准轮辋上,充以下表中规定的气压,将轮胎轮辋组合体在38℃士3℃的温度下至少停放3h。轮胎按GB/T4502(ISO10191:1993)规定的试验条件和试验方法进行耐久性试验后,轮胎气压不应低于规定的初始气压,轮胎外观检查不应有(胎面、胎侧、帘布层等)脱层、帘布层裂缝、帘线剥离、泵花、接头裂开、龟裂等缺陷。具体试验类似上述高速性能测试。
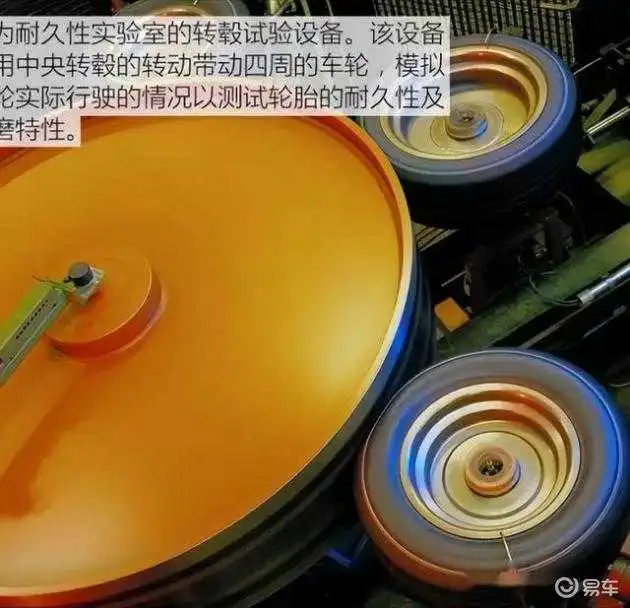
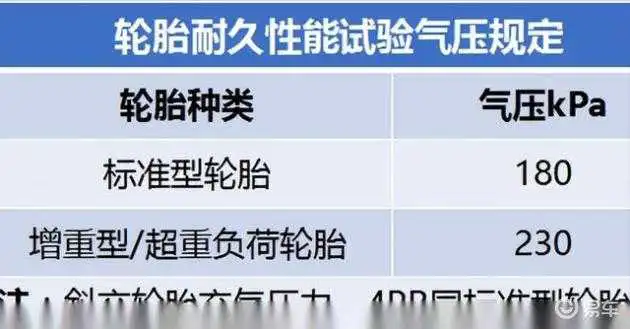
08、车轮整车匹配试验
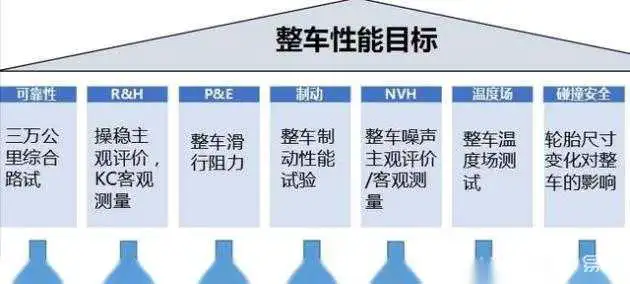
你还知道哪些汽车车轮的相关的知识,欢迎在评论区留言,我是汽车设计工匠,我们下期再聊。
汽车车轮的设计要求有哪些?在进行汽车车轮设计过程当中,我们需要制作哪些实验?这些实验需要满足哪些要求?所有的这一切都是我们进行车轮设计的核心的关键环节。大家好,我是汽车设计工匠。我们今天接着之前的课程来讲解汽车车轮的相关知识。
01、车轮密封性
将试验用未经过涂装的车轮的气门嘴孔密封,车轮的两侧面用带有密封垫的压板压紧,使其密封,再将整个车轮浸入盛满水的水箱内。试验时,充入的压缩空气压力应≥400kPa,充气达到规定气压后30s内,车轮轮辋任何部位不能有任何气泡逸出。
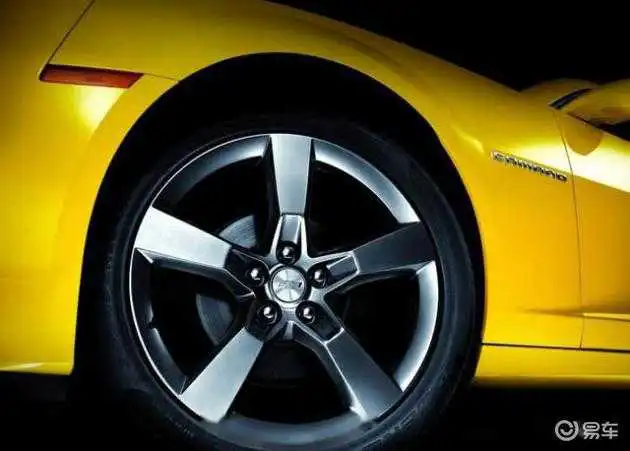
02、车轮的冲击试验
试验环境温度为10℃~38℃,试验设备按GB/T15704-1995中的相应条款规定进行,试验用的轮胎选用整车规定的与之匹配的轮胎,试验方法按GB/T15704中的相应条款规定进行。
试验完后,出现下列情况之一即判定为损坏:轮辐的任一断面处有目测可见的穿透裂纹;轮辐从轮辋上分离;轮胎气压在一分钟内漏尽。
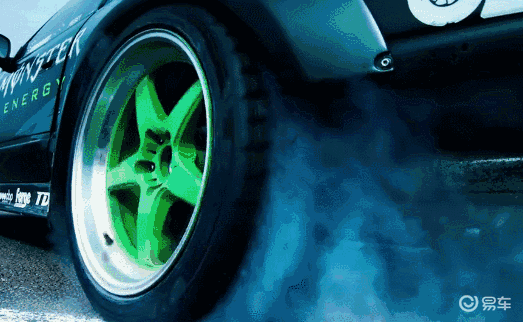
具体试验如下:
a. 轮胎的充气压力必须按车辆制造厂的规定,如无此规定,可按 200kPa充气。
b. 冲头质量为D,确定公式:D=0.6W/180。
式中: D—冲头质量 ±2%;W—最大车轮静载荷,kg
c. 把试验车轮轮胎总成安装在与车辆轮毂一致的连接盘上。车轮安装时,要按车辆或车轮制造厂推荐的方法或用手工拧紧至规定值。
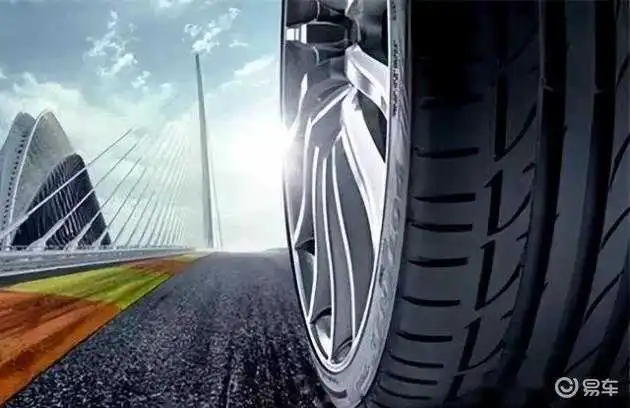
d. 调整冲头下落高度,冲头的下落高度应在轮辋轮缘的最高点上方230±2mm。
e. 调整冲头对车轮的冲击位置,冲头置于轮胎上方,其带有圆角的冲击面刃缘应与轮辋轮缘重叠 25±1mm。
f. 利用试验设备的快速释放机构,让冲头落下,冲击车轮轮胎总成。
03、轮胎尺寸要求
根据整车规定初步选定所需车轮的规格尺寸(主要是轮辋轮辐的参数)和轮胎的规格,此时应综合考虑车轮、轮胎的供应商和GB/T2978《轿车轮胎系列》来设计匹配,选择轮胎时还应考虑到轮胎的负荷指数、侧偏刚度、速度级别以及胎面花纹,以及轮胎的3c认证及美国的DOT认证等。同时,必须考虑所开发或选用的车轮和轮胎之间的匹配性。
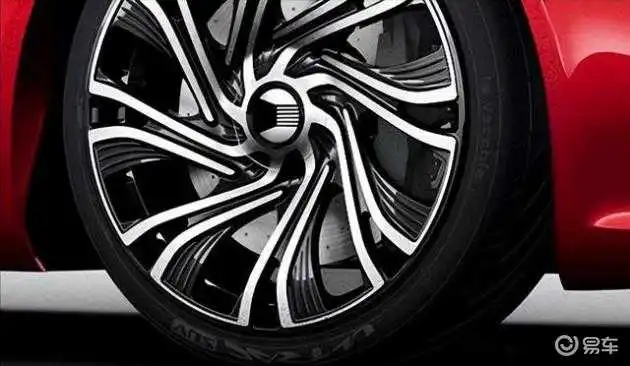
04、轮胎强度
试验室温度应保持在18℃~36℃;其他试验条件、试验方法按照GB/T4053-1996中相应规定执行,试验后轮胎的强度试验破坏能应不低于下表中规定。
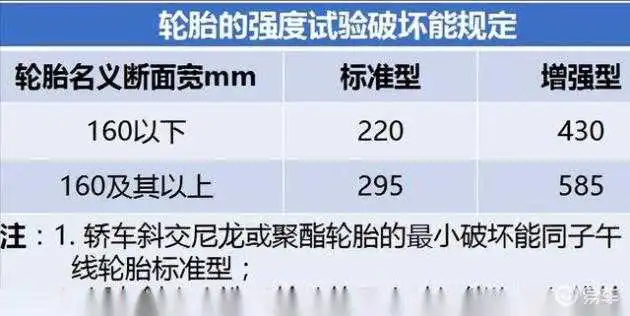
具体试验如下:
a. 将试验轮胎充入规定气压,在试验室温度下至少停放3h后,再重新调到规定气压。
b. 将轮胎固定在试验机上,沿轮胎胎面中心线取大致间隔相等的5个点进行试验。
c. 压头垂直于胎面,并压在靠近胎面圆周中心线的花纹块上,避免压入花纹沟中。
d. 测量每个点的轮胎破坏前瞬时的压力和压入探度(行程),或压头触及轮辆的瞬时压力和行程。在转入下一个点试验前校正气压。

e. 采用自动计算破坏能装置时,当达到规定的最小破坏能后,立即停止压头继续压入轮胎。
f. 如果压头触及轮辋,轮胎未压穿,且未达到最小破坏能值,则此点视为达到最小破坏能。
试验过程中,如果无内胎轮胎无法保持充气压力,允许装入内胎。
g. 计算各点的破坏能:W=F*P/2000。
注:F表示作用力N,P表示行程mm
h. 计算出各点的破坏能的算术平均值,作为该轮胎的破坏能。
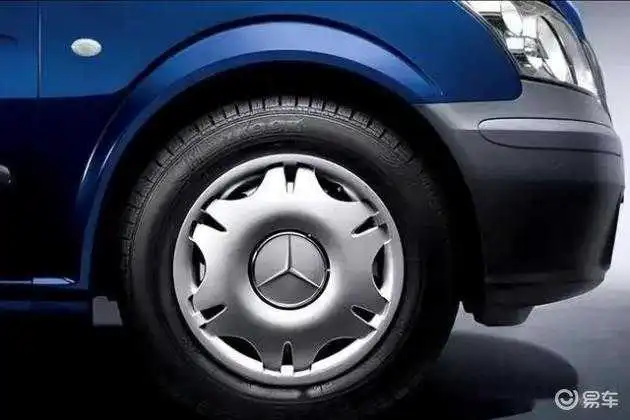
05、脱圈阻力(检查轮胎和轮辋结合紧密程度)
轮胎经GB/T4504(ISO10191:1993)中规定的试验条件和试验方法进行轮胎脱圈阻力试验,每点的脱圈阻力值应不低于下表相应的规定值。
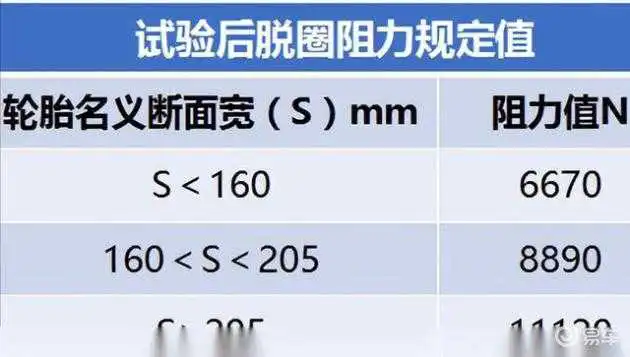
具体试验如下:
a. 将轮胎轮组合体在18℃-36℃的温度下至少停放3h后,再重新调到规定气压。
b. 将轮胎轮辋组合体安装在脱圈阻力试验机上,按规定距离调整脱圈压块的位置。
c. 在轮胎胎侧圆周面上确定至少4 个等间隔点,逐点进行试验。
d. 脱圈压块以规定的下降速度,向胎侧外表面施加压力,直到轮胎与轮辋脱开或达到下表规定的最小脱圈阻力值时为止。记录脱圈时或停止试验时的阻力值。
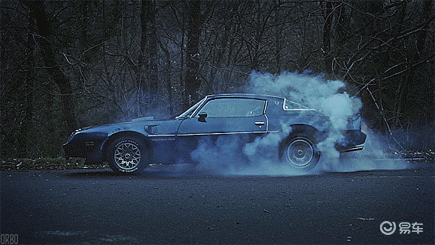
06、高速性能(转鼓法)
轮胎安装在符合规定的标准轮辋上,按下表中规定的气压充气;试验室温度应保持在38℃±3℃。按GB/T7034(ISO10191:1993)进行试验后,轮胎气压不应低于规定的初始气压;轮胎外观检查不应有(胎面、胎侧、帘布层、气密层、带束层、胎圈)脱层,帘布层裂缝、帘线剥离、帘线断裂、崩花、接头裂开、龟裂等缺陷。
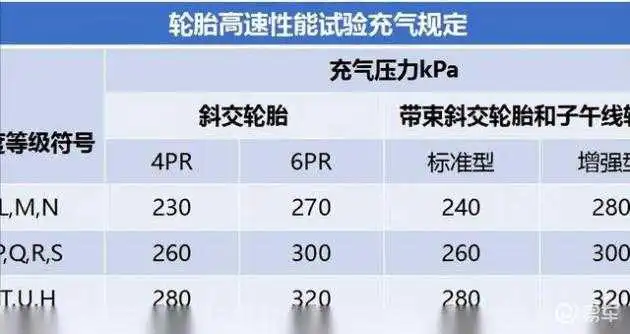
具体试验如下:
a. 将轮胎轮辋组合体在38C士3℃的温度下至少停放3h。
b. 转鼓以匀加速启动到初始试验速度的时间应在10min以内。
c. 其他试验阶段改变速度到速度稳定,所需时间小于1min。
d. 将停放后的轮胎气压重新调整到规定值,再停放15min后,测量轮胎主要尺寸。
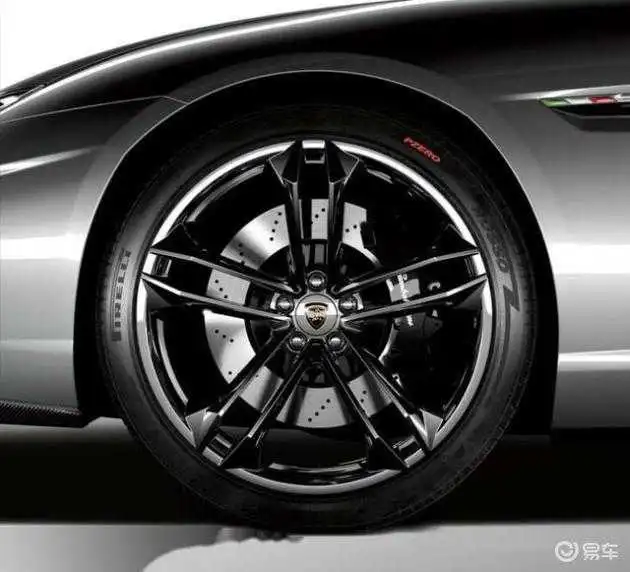
e. 将按上述条件准备好的轮胎轮辋组合体安装在试验轴上,使之垂直转鼓外表面加压,并按规定条件进行试验。
f. 试验按规定程序连续进行,其间不得中断,不得重新调整气压,试验负荷必须保持不变。
g. 轮胎按规定程序完成试验后,要立即停机测量轮胎的气压和主要尺寸,待自然冷却1h后,放掉气压,卸下轮胎进行外观检查。
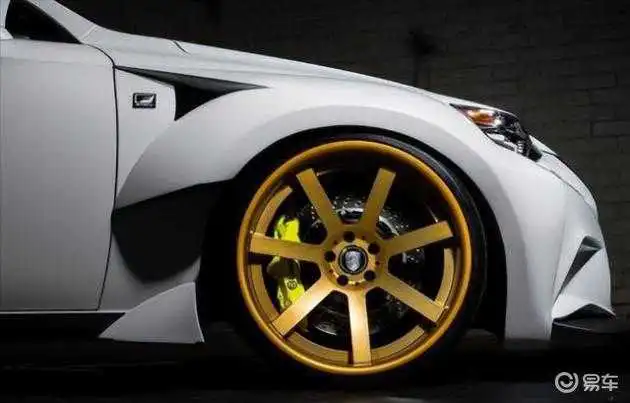
07、耐久性能(转鼓法检查轮胎高负荷连续运行能力)
轮胎安装在符合规定的标准轮辋上,充以下表中规定的气压,将轮胎轮辋组合体在38℃士3℃的温度下至少停放3h。轮胎按GB/T4502(ISO10191:1993)规定的试验条件和试验方法进行耐久性试验后,轮胎气压不应低于规定的初始气压,轮胎外观检查不应有(胎面、胎侧、帘布层等)脱层、帘布层裂缝、帘线剥离、泵花、接头裂开、龟裂等缺陷。具体试验类似上述高速性能测试。
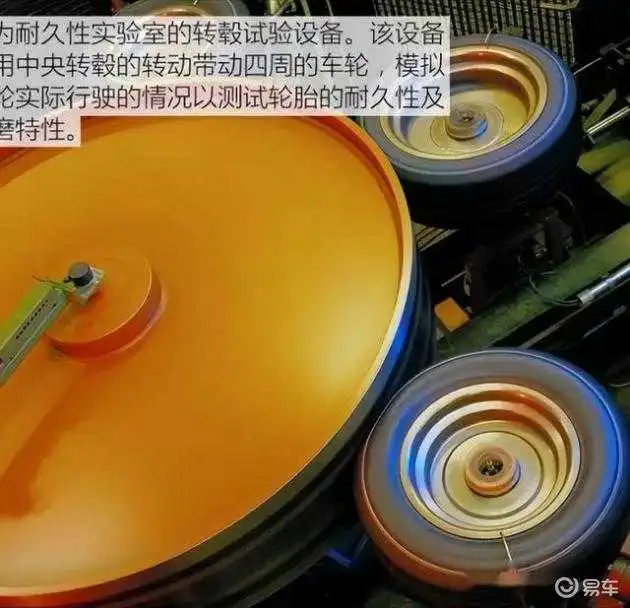
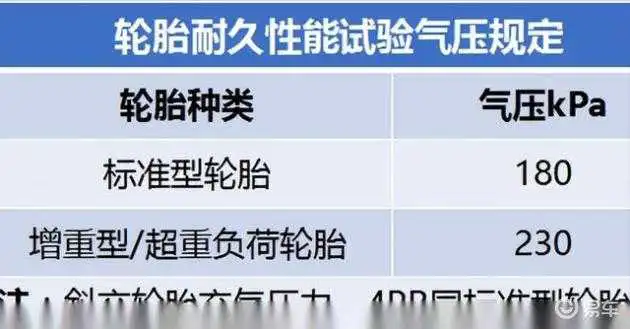
08、车轮整车匹配试验
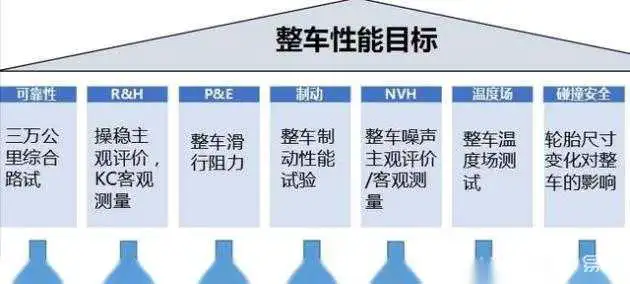
你还知道哪些汽车车轮的相关的知识,欢迎在评论区留言,我是汽车设计工匠,我们下期再聊。
汽车车轮的设计要求有哪些?在进行汽车车轮设计过程当中,我们需要制作哪些实验?这些实验需要满足哪些要求?所有的这一切都是我们进行车轮设计的核心的关键环节。大家好,我是汽车设计工匠。我们今天接着之前的课程来讲解汽车车轮的相关知识。
01、车轮密封性
将试验用未经过涂装的车轮的气门嘴孔密封,车轮的两侧面用带有密封垫的压板压紧,使其密封,再将整个车轮浸入盛满水的水箱内。试验时,充入的压缩空气压力应≥400kPa,充气达到规定气压后30s内,车轮轮辋任何部位不能有任何气泡逸出。
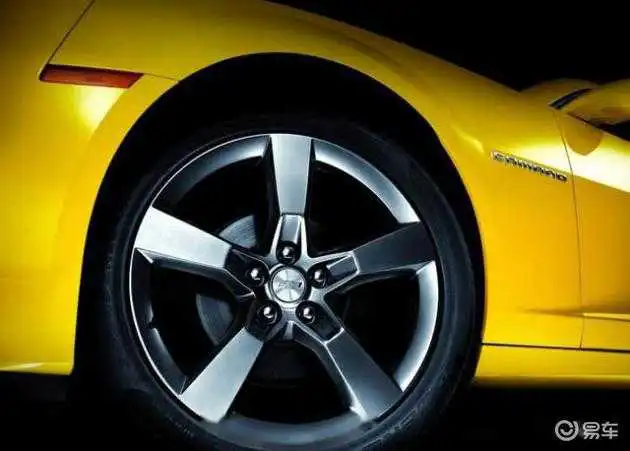
02、车轮的冲击试验
试验环境温度为10℃~38℃,试验设备按GB/T15704-1995中的相应条款规定进行,试验用的轮胎选用整车规定的与之匹配的轮胎,试验方法按GB/T15704中的相应条款规定进行。
试验完后,出现下列情况之一即判定为损坏:轮辐的任一断面处有目测可见的穿透裂纹;轮辐从轮辋上分离;轮胎气压在一分钟内漏尽。
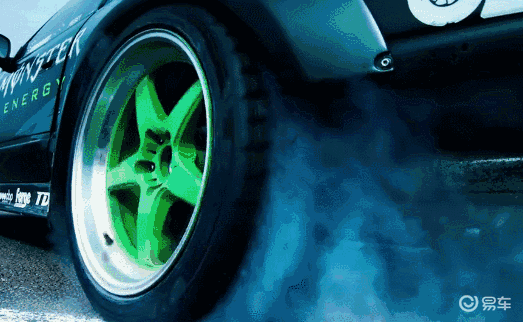
具体试验如下:
a. 轮胎的充气压力必须按车辆制造厂的规定,如无此规定,可按 200kPa充气。
b. 冲头质量为D,确定公式:D=0.6W/180。
式中: D—冲头质量 ±2%;W—最大车轮静载荷,kg
c. 把试验车轮轮胎总成安装在与车辆轮毂一致的连接盘上。车轮安装时,要按车辆或车轮制造厂推荐的方法或用手工拧紧至规定值。
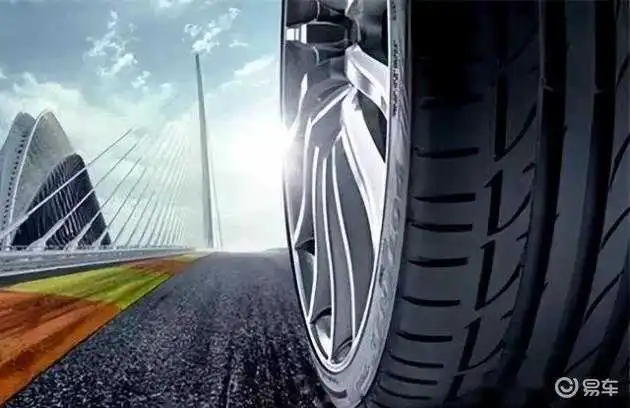
d. 调整冲头下落高度,冲头的下落高度应在轮辋轮缘的最高点上方230±2mm。
e. 调整冲头对车轮的冲击位置,冲头置于轮胎上方,其带有圆角的冲击面刃缘应与轮辋轮缘重叠 25±1mm。
f. 利用试验设备的快速释放机构,让冲头落下,冲击车轮轮胎总成。
03、轮胎尺寸要求
根据整车规定初步选定所需车轮的规格尺寸(主要是轮辋轮辐的参数)和轮胎的规格,此时应综合考虑车轮、轮胎的供应商和GB/T2978《轿车轮胎系列》来设计匹配,选择轮胎时还应考虑到轮胎的负荷指数、侧偏刚度、速度级别以及胎面花纹,以及轮胎的3c认证及美国的DOT认证等。同时,必须考虑所开发或选用的车轮和轮胎之间的匹配性。
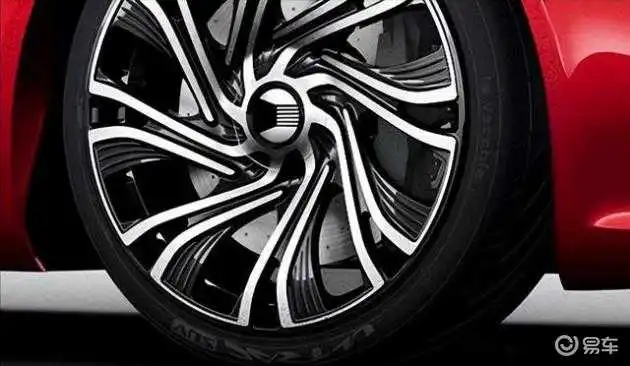
04、轮胎强度
试验室温度应保持在18℃~36℃;其他试验条件、试验方法按照GB/T4053-1996中相应规定执行,试验后轮胎的强度试验破坏能应不低于下表中规定。
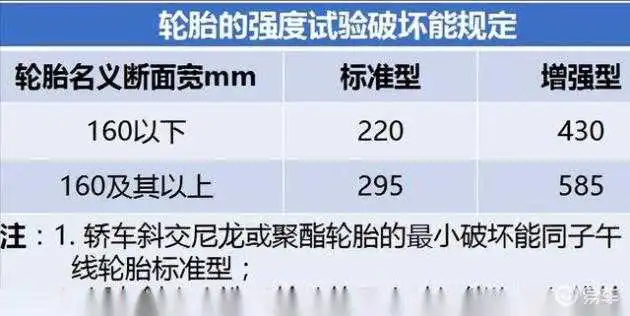
具体试验如下:
a. 将试验轮胎充入规定气压,在试验室温度下至少停放3h后,再重新调到规定气压。
b. 将轮胎固定在试验机上,沿轮胎胎面中心线取大致间隔相等的5个点进行试验。
c. 压头垂直于胎面,并压在靠近胎面圆周中心线的花纹块上,避免压入花纹沟中。
d. 测量每个点的轮胎破坏前瞬时的压力和压入探度(行程),或压头触及轮辆的瞬时压力和行程。在转入下一个点试验前校正气压。

e. 采用自动计算破坏能装置时,当达到规定的最小破坏能后,立即停止压头继续压入轮胎。
f. 如果压头触及轮辋,轮胎未压穿,且未达到最小破坏能值,则此点视为达到最小破坏能。
试验过程中,如果无内胎轮胎无法保持充气压力,允许装入内胎。
g. 计算各点的破坏能:W=F*P/2000。
注:F表示作用力N,P表示行程mm
h. 计算出各点的破坏能的算术平均值,作为该轮胎的破坏能。
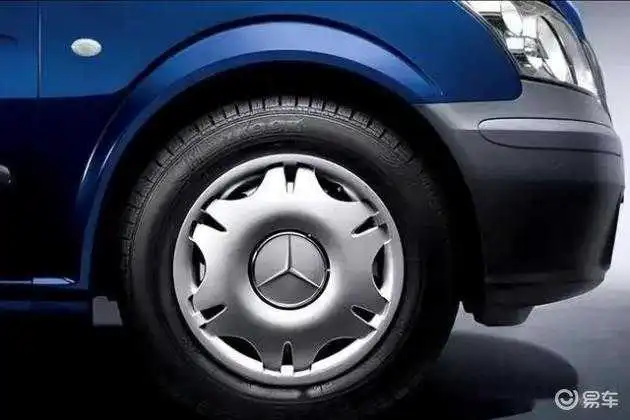
05、脱圈阻力(检查轮胎和轮辋结合紧密程度)
轮胎经GB/T4504(ISO10191:1993)中规定的试验条件和试验方法进行轮胎脱圈阻力试验,每点的脱圈阻力值应不低于下表相应的规定值。
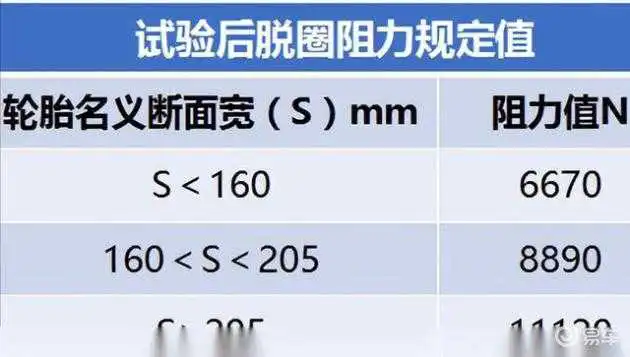
具体试验如下:
a. 将轮胎轮组合体在18℃-36℃的温度下至少停放3h后,再重新调到规定气压。
b. 将轮胎轮辋组合体安装在脱圈阻力试验机上,按规定距离调整脱圈压块的位置。
c. 在轮胎胎侧圆周面上确定至少4 个等间隔点,逐点进行试验。
d. 脱圈压块以规定的下降速度,向胎侧外表面施加压力,直到轮胎与轮辋脱开或达到下表规定的最小脱圈阻力值时为止。记录脱圈时或停止试验时的阻力值。
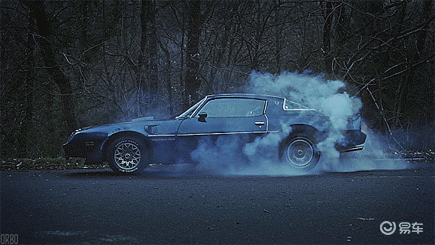
06、高速性能(转鼓法)
轮胎安装在符合规定的标准轮辋上,按下表中规定的气压充气;试验室温度应保持在38℃±3℃。按GB/T7034(ISO10191:1993)进行试验后,轮胎气压不应低于规定的初始气压;轮胎外观检查不应有(胎面、胎侧、帘布层、气密层、带束层、胎圈)脱层,帘布层裂缝、帘线剥离、帘线断裂、崩花、接头裂开、龟裂等缺陷。
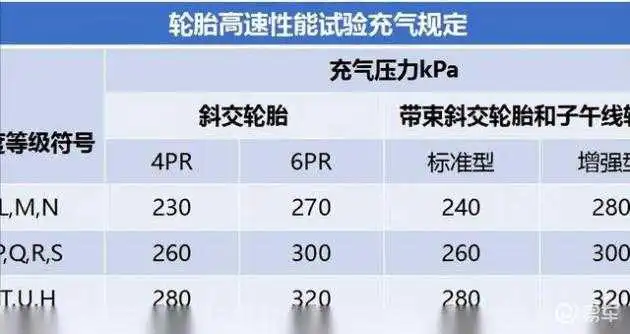
具体试验如下:
a. 将轮胎轮辋组合体在38C士3℃的温度下至少停放3h。
b. 转鼓以匀加速启动到初始试验速度的时间应在10min以内。
c. 其他试验阶段改变速度到速度稳定,所需时间小于1min。
d. 将停放后的轮胎气压重新调整到规定值,再停放15min后,测量轮胎主要尺寸。
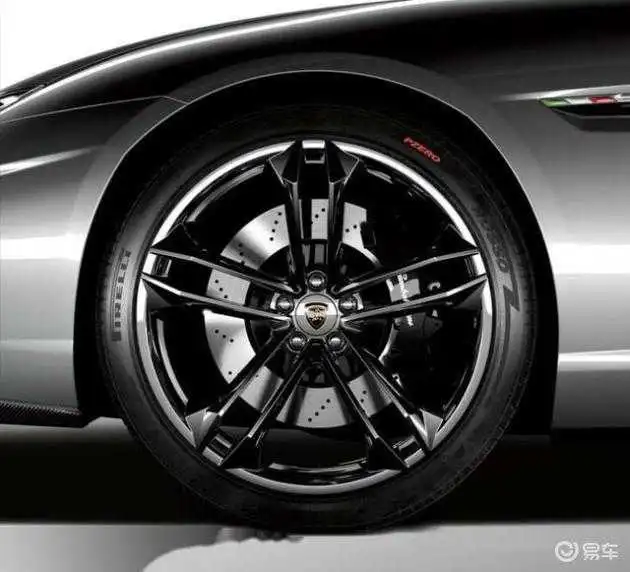
e. 将按上述条件准备好的轮胎轮辋组合体安装在试验轴上,使之垂直转鼓外表面加压,并按规定条件进行试验。
f. 试验按规定程序连续进行,其间不得中断,不得重新调整气压,试验负荷必须保持不变。
g. 轮胎按规定程序完成试验后,要立即停机测量轮胎的气压和主要尺寸,待自然冷却1h后,放掉气压,卸下轮胎进行外观检查。
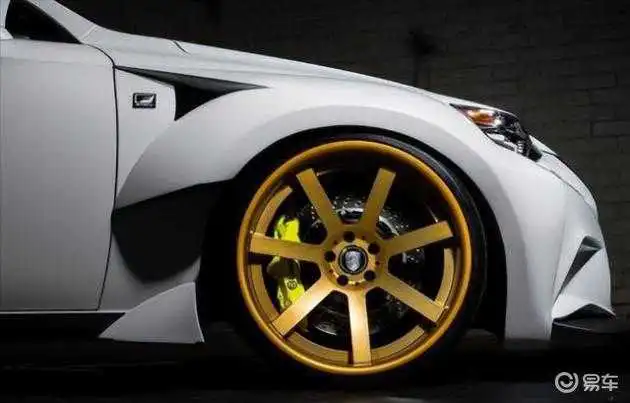
07、耐久性能(转鼓法检查轮胎高负荷连续运行能力)
轮胎安装在符合规定的标准轮辋上,充以下表中规定的气压,将轮胎轮辋组合体在38℃士3℃的温度下至少停放3h。轮胎按GB/T4502(ISO10191:1993)规定的试验条件和试验方法进行耐久性试验后,轮胎气压不应低于规定的初始气压,轮胎外观检查不应有(胎面、胎侧、帘布层等)脱层、帘布层裂缝、帘线剥离、泵花、接头裂开、龟裂等缺陷。具体试验类似上述高速性能测试。
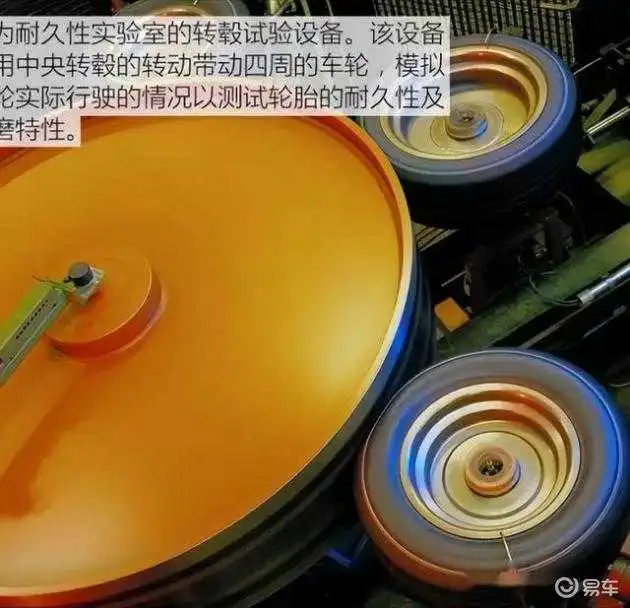
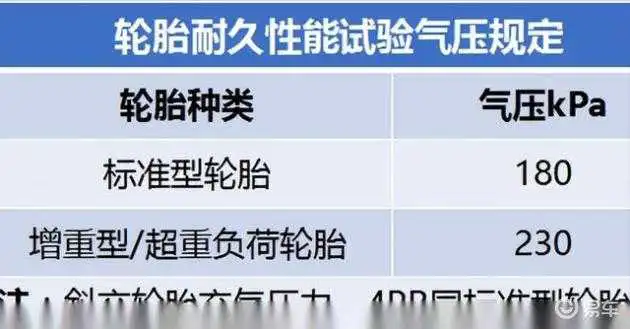
08、车轮整车匹配试验
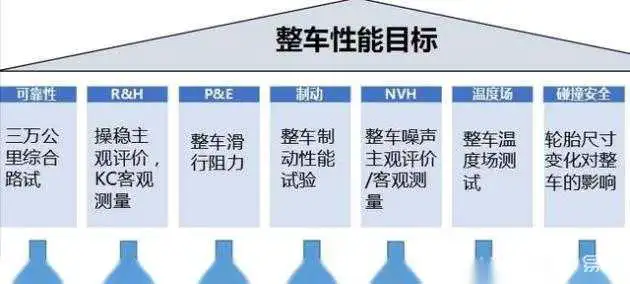
你还知道哪些汽车车轮的相关的知识,欢迎在评论区留言,我是汽车设计工匠,我们下期再聊。
汽车车轮的设计要求有哪些?在进行汽车车轮设计过程当中,我们需要制作哪些实验?这些实验需要满足哪些要求?所有的这一切都是我们进行车轮设计的核心的关键环节。大家好,我是汽车设计工匠。我们今天接着之前的课程来讲解汽车车轮的相关知识。
01、车轮密封性
将试验用未经过涂装的车轮的气门嘴孔密封,车轮的两侧面用带有密封垫的压板压紧,使其密封,再将整个车轮浸入盛满水的水箱内。试验时,充入的压缩空气压力应≥400kPa,充气达到规定气压后30s内,车轮轮辋任何部位不能有任何气泡逸出。
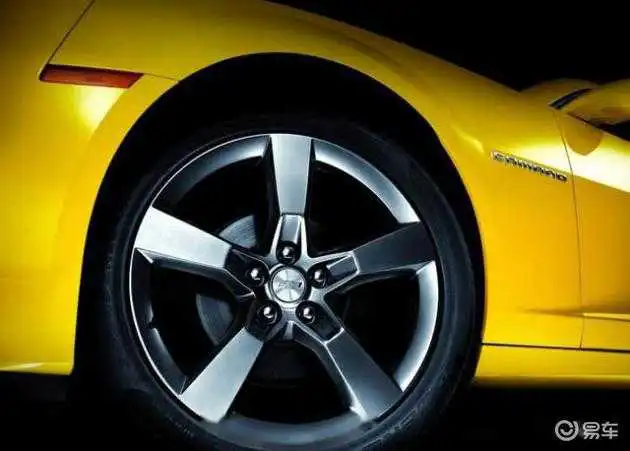
02、车轮的冲击试验
试验环境温度为10℃~38℃,试验设备按GB/T15704-1995中的相应条款规定进行,试验用的轮胎选用整车规定的与之匹配的轮胎,试验方法按GB/T15704中的相应条款规定进行。
试验完后,出现下列情况之一即判定为损坏:轮辐的任一断面处有目测可见的穿透裂纹;轮辐从轮辋上分离;轮胎气压在一分钟内漏尽。
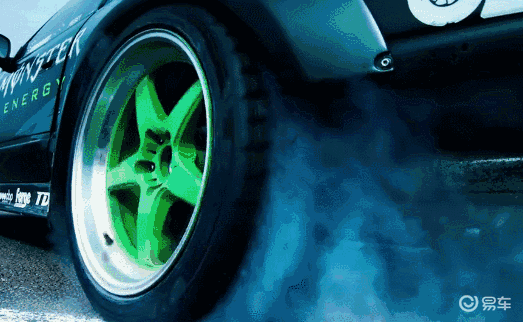
具体试验如下:
a. 轮胎的充气压力必须按车辆制造厂的规定,如无此规定,可按 200kPa充气。
b. 冲头质量为D,确定公式:D=0.6W/180。
式中: D—冲头质量 ±2%;W—最大车轮静载荷,kg
c. 把试验车轮轮胎总成安装在与车辆轮毂一致的连接盘上。车轮安装时,要按车辆或车轮制造厂推荐的方法或用手工拧紧至规定值。
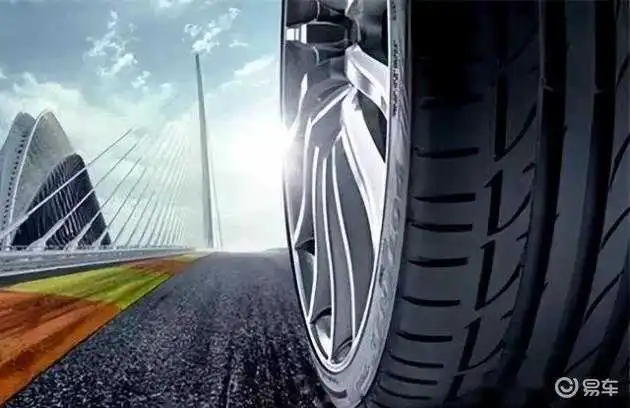
d. 调整冲头下落高度,冲头的下落高度应在轮辋轮缘的最高点上方230±2mm。
e. 调整冲头对车轮的冲击位置,冲头置于轮胎上方,其带有圆角的冲击面刃缘应与轮辋轮缘重叠 25±1mm。
f. 利用试验设备的快速释放机构,让冲头落下,冲击车轮轮胎总成。
03、轮胎尺寸要求
根据整车规定初步选定所需车轮的规格尺寸(主要是轮辋轮辐的参数)和轮胎的规格,此时应综合考虑车轮、轮胎的供应商和GB/T2978《轿车轮胎系列》来设计匹配,选择轮胎时还应考虑到轮胎的负荷指数、侧偏刚度、速度级别以及胎面花纹,以及轮胎的3c认证及美国的DOT认证等。同时,必须考虑所开发或选用的车轮和轮胎之间的匹配性。
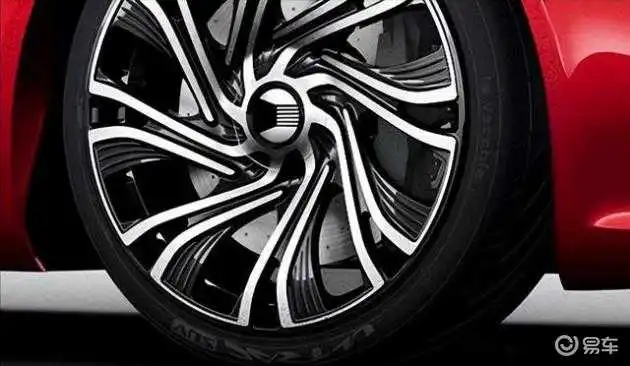
04、轮胎强度
试验室温度应保持在18℃~36℃;其他试验条件、试验方法按照GB/T4053-1996中相应规定执行,试验后轮胎的强度试验破坏能应不低于下表中规定。
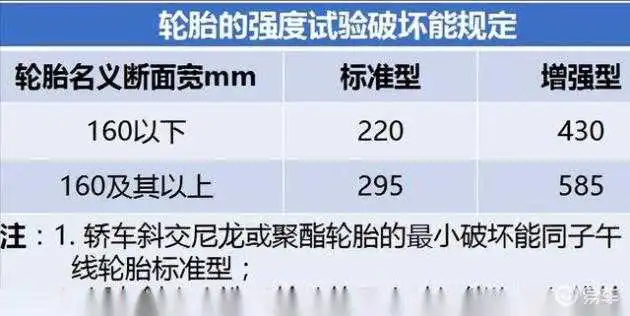
具体试验如下:
a. 将试验轮胎充入规定气压,在试验室温度下至少停放3h后,再重新调到规定气压。
b. 将轮胎固定在试验机上,沿轮胎胎面中心线取大致间隔相等的5个点进行试验。
c. 压头垂直于胎面,并压在靠近胎面圆周中心线的花纹块上,避免压入花纹沟中。
d. 测量每个点的轮胎破坏前瞬时的压力和压入探度(行程),或压头触及轮辆的瞬时压力和行程。在转入下一个点试验前校正气压。

e. 采用自动计算破坏能装置时,当达到规定的最小破坏能后,立即停止压头继续压入轮胎。
f. 如果压头触及轮辋,轮胎未压穿,且未达到最小破坏能值,则此点视为达到最小破坏能。
试验过程中,如果无内胎轮胎无法保持充气压力,允许装入内胎。
g. 计算各点的破坏能:W=F*P/2000。
注:F表示作用力N,P表示行程mm
h. 计算出各点的破坏能的算术平均值,作为该轮胎的破坏能。
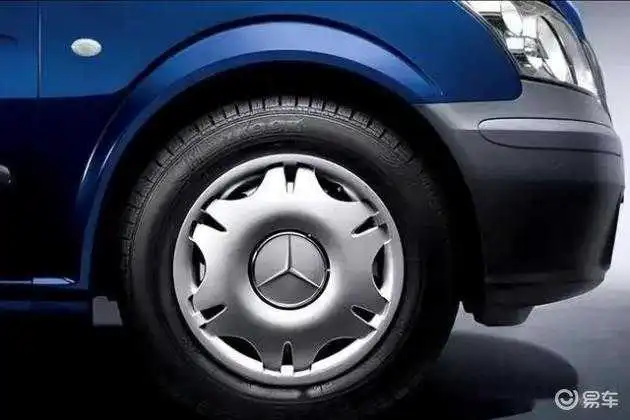
05、脱圈阻力(检查轮胎和轮辋结合紧密程度)
轮胎经GB/T4504(ISO10191:1993)中规定的试验条件和试验方法进行轮胎脱圈阻力试验,每点的脱圈阻力值应不低于下表相应的规定值。
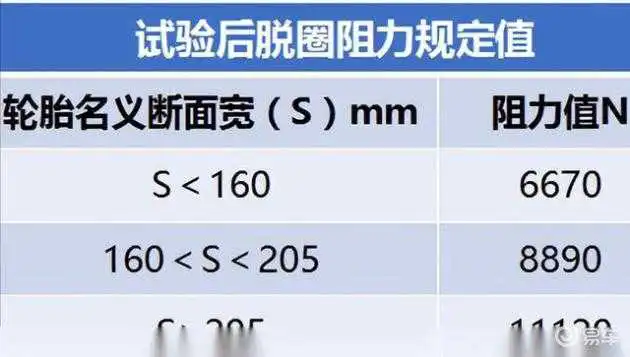
具体试验如下:
a. 将轮胎轮组合体在18℃-36℃的温度下至少停放3h后,再重新调到规定气压。
b. 将轮胎轮辋组合体安装在脱圈阻力试验机上,按规定距离调整脱圈压块的位置。
c. 在轮胎胎侧圆周面上确定至少4 个等间隔点,逐点进行试验。
d. 脱圈压块以规定的下降速度,向胎侧外表面施加压力,直到轮胎与轮辋脱开或达到下表规定的最小脱圈阻力值时为止。记录脱圈时或停止试验时的阻力值。
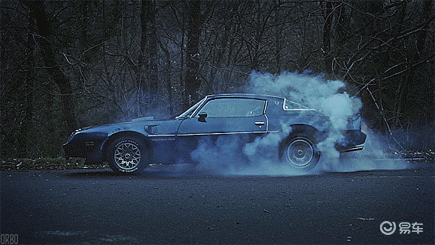
06、高速性能(转鼓法)
轮胎安装在符合规定的标准轮辋上,按下表中规定的气压充气;试验室温度应保持在38℃±3℃。按GB/T7034(ISO10191:1993)进行试验后,轮胎气压不应低于规定的初始气压;轮胎外观检查不应有(胎面、胎侧、帘布层、气密层、带束层、胎圈)脱层,帘布层裂缝、帘线剥离、帘线断裂、崩花、接头裂开、龟裂等缺陷。
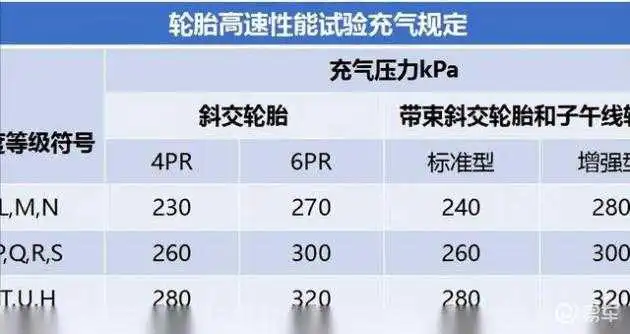
具体试验如下:
a. 将轮胎轮辋组合体在38C士3℃的温度下至少停放3h。
b. 转鼓以匀加速启动到初始试验速度的时间应在10min以内。
c. 其他试验阶段改变速度到速度稳定,所需时间小于1min。
d. 将停放后的轮胎气压重新调整到规定值,再停放15min后,测量轮胎主要尺寸。
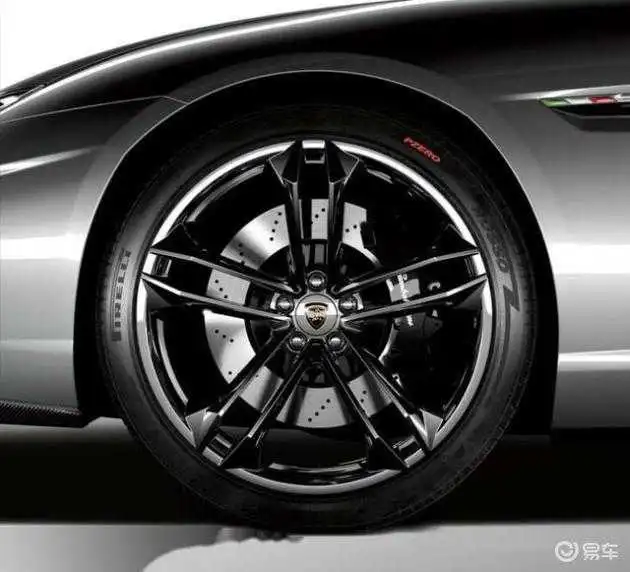
e. 将按上述条件准备好的轮胎轮辋组合体安装在试验轴上,使之垂直转鼓外表面加压,并按规定条件进行试验。
f. 试验按规定程序连续进行,其间不得中断,不得重新调整气压,试验负荷必须保持不变。
g. 轮胎按规定程序完成试验后,要立即停机测量轮胎的气压和主要尺寸,待自然冷却1h后,放掉气压,卸下轮胎进行外观检查。
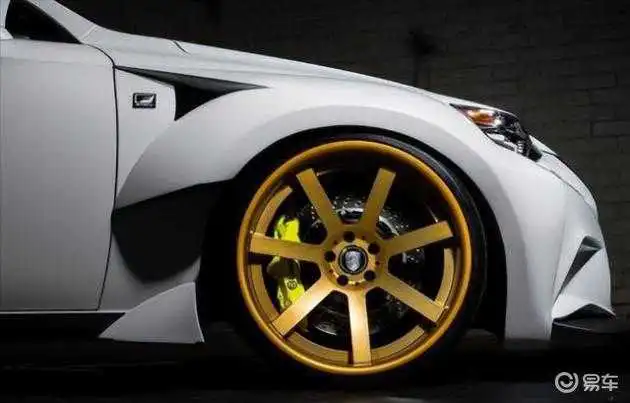
07、耐久性能(转鼓法检查轮胎高负荷连续运行能力)
轮胎安装在符合规定的标准轮辋上,充以下表中规定的气压,将轮胎轮辋组合体在38℃士3℃的温度下至少停放3h。轮胎按GB/T4502(ISO10191:1993)规定的试验条件和试验方法进行耐久性试验后,轮胎气压不应低于规定的初始气压,轮胎外观检查不应有(胎面、胎侧、帘布层等)脱层、帘布层裂缝、帘线剥离、泵花、接头裂开、龟裂等缺陷。具体试验类似上述高速性能测试。
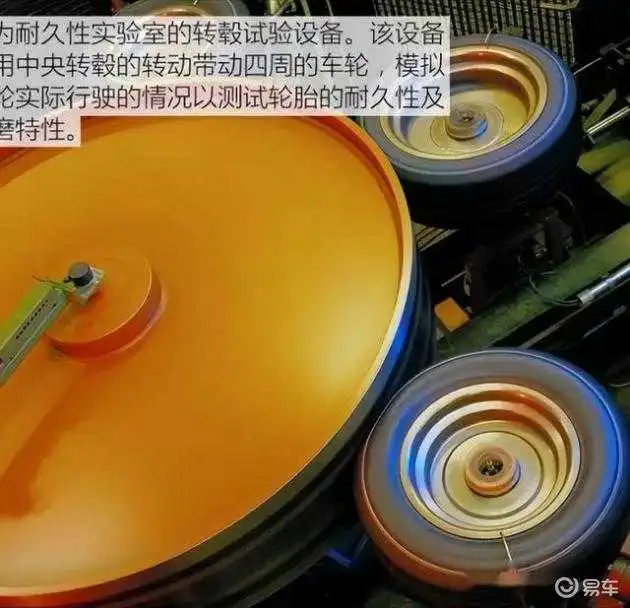
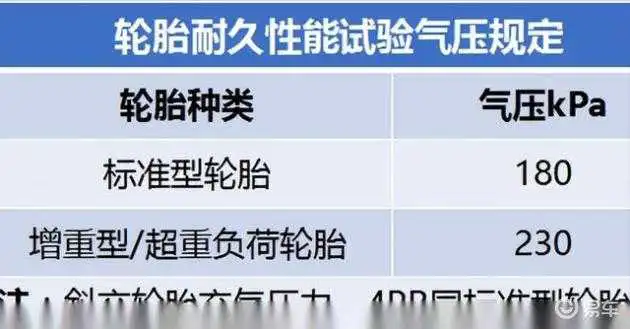
08、车轮整车匹配试验
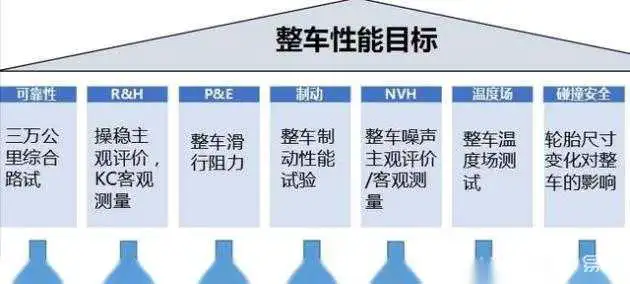
你还知道哪些汽车车轮的相关的知识,欢迎在评论区留言,我是汽车设计工匠,我们下期再聊。
汽车车轮的设计要求有哪些?在进行汽车车轮设计过程当中,我们需要制作哪些实验?这些实验需要满足哪些要求?所有的这一切都是我们进行车轮设计的核心的关键环节。大家好,我是汽车设计工匠。我们今天接着之前的课程来讲解汽车车轮的相关知识。
01、车轮密封性
将试验用未经过涂装的车轮的气门嘴孔密封,车轮的两侧面用带有密封垫的压板压紧,使其密封,再将整个车轮浸入盛满水的水箱内。试验时,充入的压缩空气压力应≥400kPa,充气达到规定气压后30s内,车轮轮辋任何部位不能有任何气泡逸出。
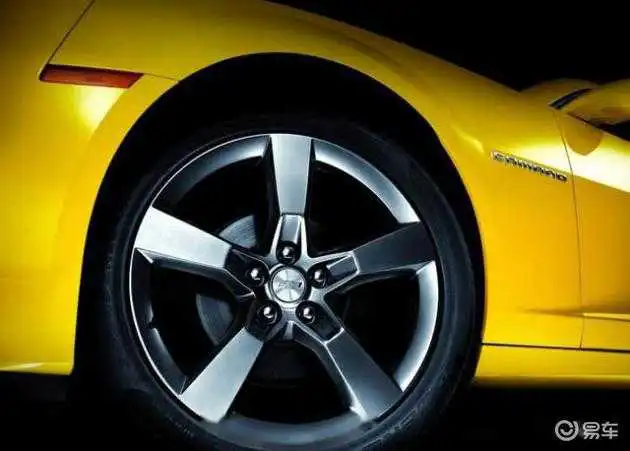
02、车轮的冲击试验
试验环境温度为10℃~38℃,试验设备按GB/T15704-1995中的相应条款规定进行,试验用的轮胎选用整车规定的与之匹配的轮胎,试验方法按GB/T15704中的相应条款规定进行。
试验完后,出现下列情况之一即判定为损坏:轮辐的任一断面处有目测可见的穿透裂纹;轮辐从轮辋上分离;轮胎气压在一分钟内漏尽。
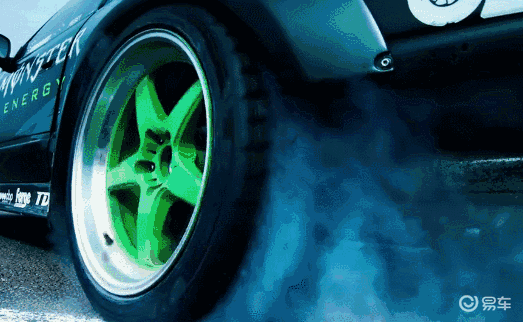
具体试验如下:
a. 轮胎的充气压力必须按车辆制造厂的规定,如无此规定,可按 200kPa充气。
b. 冲头质量为D,确定公式:D=0.6W/180。
式中: D—冲头质量 ±2%;W—最大车轮静载荷,kg
c. 把试验车轮轮胎总成安装在与车辆轮毂一致的连接盘上。车轮安装时,要按车辆或车轮制造厂推荐的方法或用手工拧紧至规定值。
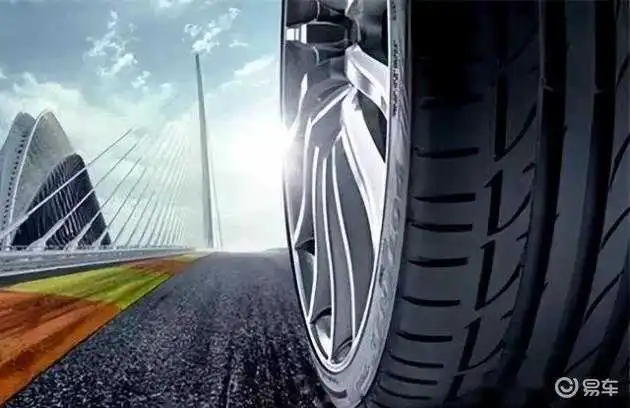
d. 调整冲头下落高度,冲头的下落高度应在轮辋轮缘的最高点上方230±2mm。
e. 调整冲头对车轮的冲击位置,冲头置于轮胎上方,其带有圆角的冲击面刃缘应与轮辋轮缘重叠 25±1mm。
f. 利用试验设备的快速释放机构,让冲头落下,冲击车轮轮胎总成。
03、轮胎尺寸要求
根据整车规定初步选定所需车轮的规格尺寸(主要是轮辋轮辐的参数)和轮胎的规格,此时应综合考虑车轮、轮胎的供应商和GB/T2978《轿车轮胎系列》来设计匹配,选择轮胎时还应考虑到轮胎的负荷指数、侧偏刚度、速度级别以及胎面花纹,以及轮胎的3c认证及美国的DOT认证等。同时,必须考虑所开发或选用的车轮和轮胎之间的匹配性。
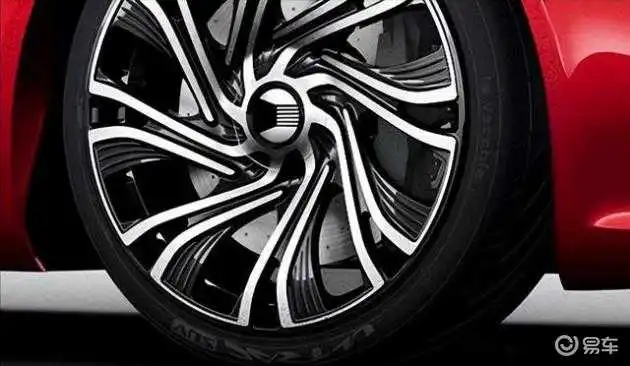
04、轮胎强度
试验室温度应保持在18℃~36℃;其他试验条件、试验方法按照GB/T4053-1996中相应规定执行,试验后轮胎的强度试验破坏能应不低于下表中规定。
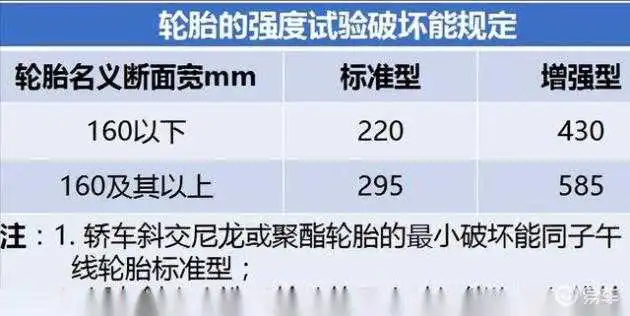
具体试验如下:
a. 将试验轮胎充入规定气压,在试验室温度下至少停放3h后,再重新调到规定气压。
b. 将轮胎固定在试验机上,沿轮胎胎面中心线取大致间隔相等的5个点进行试验。
c. 压头垂直于胎面,并压在靠近胎面圆周中心线的花纹块上,避免压入花纹沟中。
d. 测量每个点的轮胎破坏前瞬时的压力和压入探度(行程),或压头触及轮辆的瞬时压力和行程。在转入下一个点试验前校正气压。

e. 采用自动计算破坏能装置时,当达到规定的最小破坏能后,立即停止压头继续压入轮胎。
f. 如果压头触及轮辋,轮胎未压穿,且未达到最小破坏能值,则此点视为达到最小破坏能。
试验过程中,如果无内胎轮胎无法保持充气压力,允许装入内胎。
g. 计算各点的破坏能:W=F*P/2000。
注:F表示作用力N,P表示行程mm
h. 计算出各点的破坏能的算术平均值,作为该轮胎的破坏能。
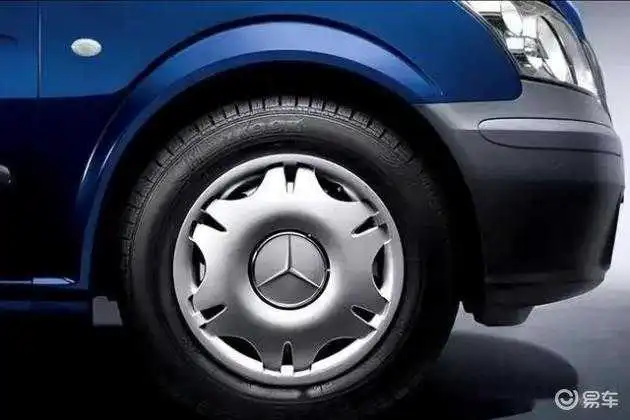
05、脱圈阻力(检查轮胎和轮辋结合紧密程度)
轮胎经GB/T4504(ISO10191:1993)中规定的试验条件和试验方法进行轮胎脱圈阻力试验,每点的脱圈阻力值应不低于下表相应的规定值。
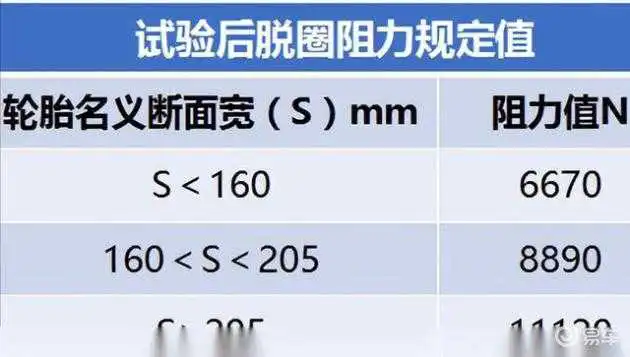
具体试验如下:
a. 将轮胎轮组合体在18℃-36℃的温度下至少停放3h后,再重新调到规定气压。
b. 将轮胎轮辋组合体安装在脱圈阻力试验机上,按规定距离调整脱圈压块的位置。
c. 在轮胎胎侧圆周面上确定至少4 个等间隔点,逐点进行试验。
d. 脱圈压块以规定的下降速度,向胎侧外表面施加压力,直到轮胎与轮辋脱开或达到下表规定的最小脱圈阻力值时为止。记录脱圈时或停止试验时的阻力值。
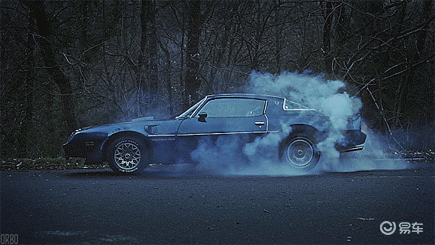
06、高速性能(转鼓法)
轮胎安装在符合规定的标准轮辋上,按下表中规定的气压充气;试验室温度应保持在38℃±3℃。按GB/T7034(ISO10191:1993)进行试验后,轮胎气压不应低于规定的初始气压;轮胎外观检查不应有(胎面、胎侧、帘布层、气密层、带束层、胎圈)脱层,帘布层裂缝、帘线剥离、帘线断裂、崩花、接头裂开、龟裂等缺陷。
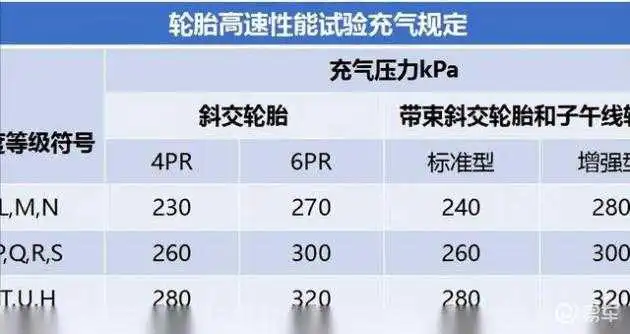
具体试验如下:
a. 将轮胎轮辋组合体在38C士3℃的温度下至少停放3h。
b. 转鼓以匀加速启动到初始试验速度的时间应在10min以内。
c. 其他试验阶段改变速度到速度稳定,所需时间小于1min。
d. 将停放后的轮胎气压重新调整到规定值,再停放15min后,测量轮胎主要尺寸。
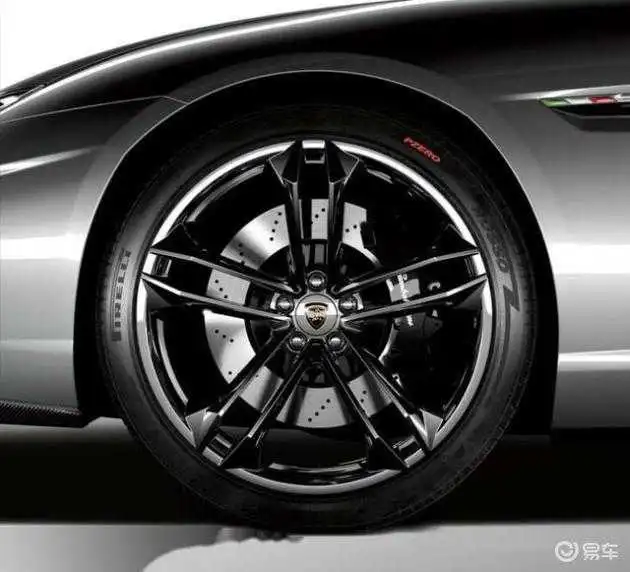
e. 将按上述条件准备好的轮胎轮辋组合体安装在试验轴上,使之垂直转鼓外表面加压,并按规定条件进行试验。
f. 试验按规定程序连续进行,其间不得中断,不得重新调整气压,试验负荷必须保持不变。
g. 轮胎按规定程序完成试验后,要立即停机测量轮胎的气压和主要尺寸,待自然冷却1h后,放掉气压,卸下轮胎进行外观检查。
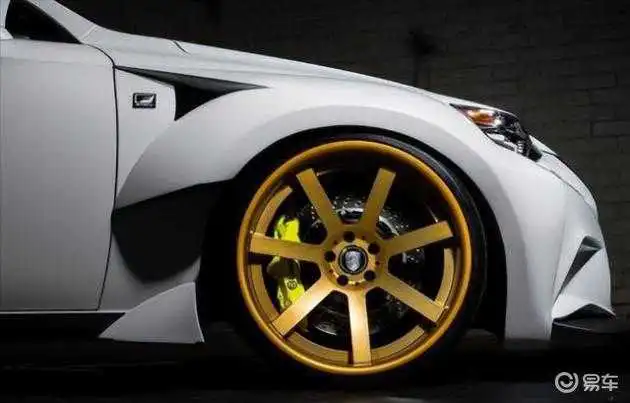
07、耐久性能(转鼓法检查轮胎高负荷连续运行能力)
轮胎安装在符合规定的标准轮辋上,充以下表中规定的气压,将轮胎轮辋组合体在38℃士3℃的温度下至少停放3h。轮胎按GB/T4502(ISO10191:1993)规定的试验条件和试验方法进行耐久性试验后,轮胎气压不应低于规定的初始气压,轮胎外观检查不应有(胎面、胎侧、帘布层等)脱层、帘布层裂缝、帘线剥离、泵花、接头裂开、龟裂等缺陷。具体试验类似上述高速性能测试。
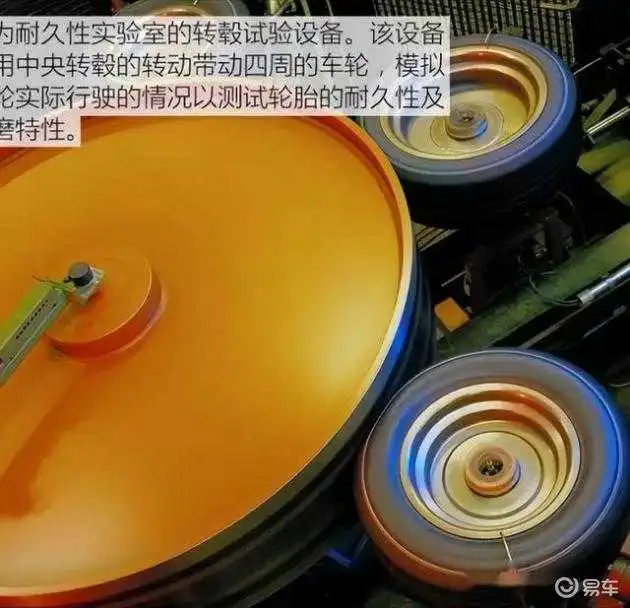
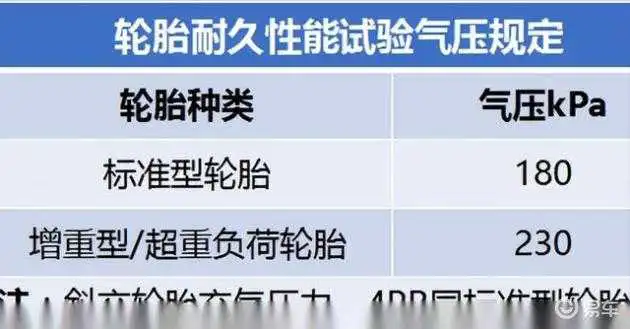
08、车轮整车匹配试验
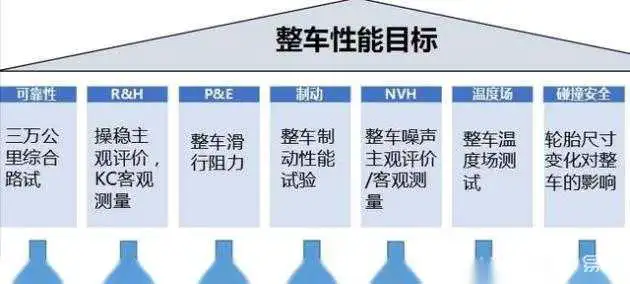
你还知道哪些汽车车轮的相关的知识,欢迎在评论区留言,我是汽车设计工匠,我们下期再聊。
汽车车轮的设计要求有哪些?在进行汽车车轮设计过程当中,我们需要制作哪些实验?这些实验需要满足哪些要求?所有的这一切都是我们进行车轮设计的核心的关键环节。大家好,我是汽车设计工匠。我们今天接着之前的课程来讲解汽车车轮的相关知识。
01、车轮密封性
将试验用未经过涂装的车轮的气门嘴孔密封,车轮的两侧面用带有密封垫的压板压紧,使其密封,再将整个车轮浸入盛满水的水箱内。试验时,充入的压缩空气压力应≥400kPa,充气达到规定气压后30s内,车轮轮辋任何部位不能有任何气泡逸出。
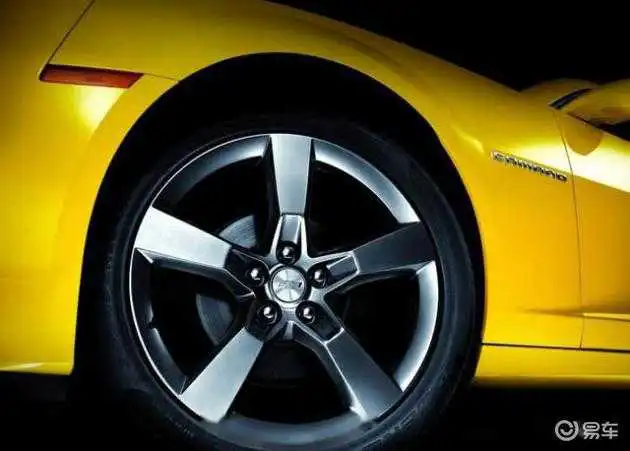
02、车轮的冲击试验
试验环境温度为10℃~38℃,试验设备按GB/T15704-1995中的相应条款规定进行,试验用的轮胎选用整车规定的与之匹配的轮胎,试验方法按GB/T15704中的相应条款规定进行。
试验完后,出现下列情况之一即判定为损坏:轮辐的任一断面处有目测可见的穿透裂纹;轮辐从轮辋上分离;轮胎气压在一分钟内漏尽。
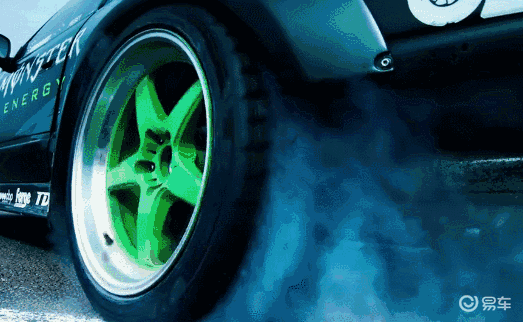
具体试验如下:
a. 轮胎的充气压力必须按车辆制造厂的规定,如无此规定,可按 200kPa充气。
b. 冲头质量为D,确定公式:D=0.6W/180。
式中: D—冲头质量 ±2%;W—最大车轮静载荷,kg
c. 把试验车轮轮胎总成安装在与车辆轮毂一致的连接盘上。车轮安装时,要按车辆或车轮制造厂推荐的方法或用手工拧紧至规定值。
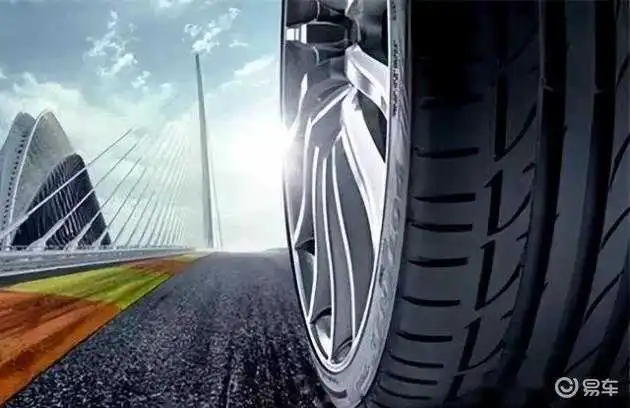
d. 调整冲头下落高度,冲头的下落高度应在轮辋轮缘的最高点上方230±2mm。
e. 调整冲头对车轮的冲击位置,冲头置于轮胎上方,其带有圆角的冲击面刃缘应与轮辋轮缘重叠 25±1mm。
f. 利用试验设备的快速释放机构,让冲头落下,冲击车轮轮胎总成。
03、轮胎尺寸要求
根据整车规定初步选定所需车轮的规格尺寸(主要是轮辋轮辐的参数)和轮胎的规格,此时应综合考虑车轮、轮胎的供应商和GB/T2978《轿车轮胎系列》来设计匹配,选择轮胎时还应考虑到轮胎的负荷指数、侧偏刚度、速度级别以及胎面花纹,以及轮胎的3c认证及美国的DOT认证等。同时,必须考虑所开发或选用的车轮和轮胎之间的匹配性。
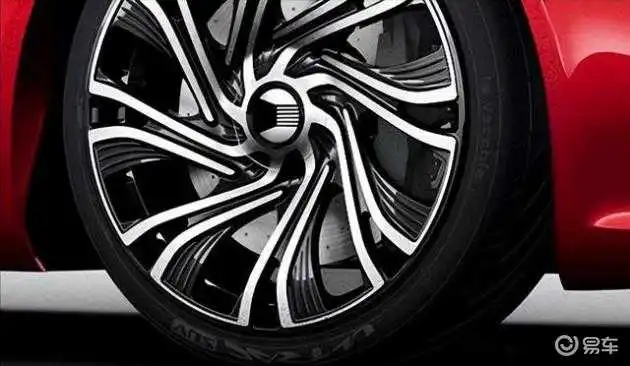
04、轮胎强度
试验室温度应保持在18℃~36℃;其他试验条件、试验方法按照GB/T4053-1996中相应规定执行,试验后轮胎的强度试验破坏能应不低于下表中规定。
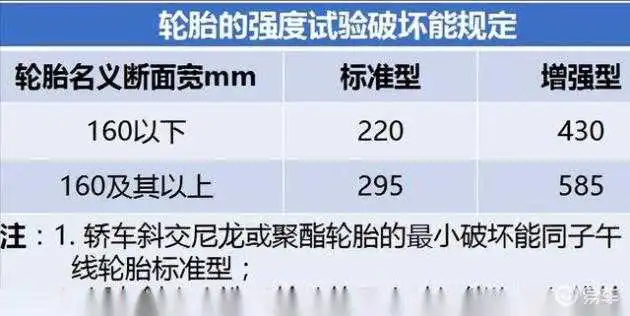
具体试验如下:
a. 将试验轮胎充入规定气压,在试验室温度下至少停放3h后,再重新调到规定气压。
b. 将轮胎固定在试验机上,沿轮胎胎面中心线取大致间隔相等的5个点进行试验。
c. 压头垂直于胎面,并压在靠近胎面圆周中心线的花纹块上,避免压入花纹沟中。
d. 测量每个点的轮胎破坏前瞬时的压力和压入探度(行程),或压头触及轮辆的瞬时压力和行程。在转入下一个点试验前校正气压。

e. 采用自动计算破坏能装置时,当达到规定的最小破坏能后,立即停止压头继续压入轮胎。
f. 如果压头触及轮辋,轮胎未压穿,且未达到最小破坏能值,则此点视为达到最小破坏能。
试验过程中,如果无内胎轮胎无法保持充气压力,允许装入内胎。
g. 计算各点的破坏能:W=F*P/2000。
注:F表示作用力N,P表示行程mm
h. 计算出各点的破坏能的算术平均值,作为该轮胎的破坏能。
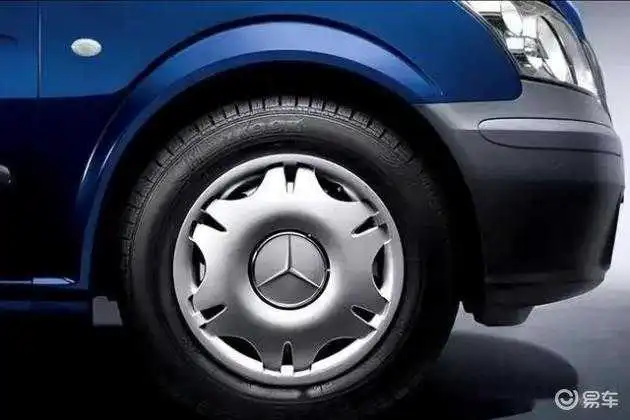
05、脱圈阻力(检查轮胎和轮辋结合紧密程度)
轮胎经GB/T4504(ISO10191:1993)中规定的试验条件和试验方法进行轮胎脱圈阻力试验,每点的脱圈阻力值应不低于下表相应的规定值。
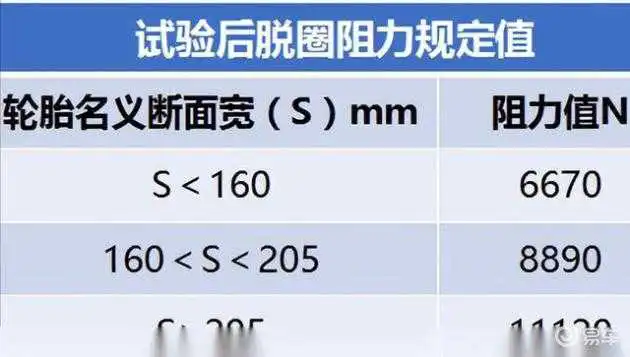
具体试验如下:
a. 将轮胎轮组合体在18℃-36℃的温度下至少停放3h后,再重新调到规定气压。
b. 将轮胎轮辋组合体安装在脱圈阻力试验机上,按规定距离调整脱圈压块的位置。
c. 在轮胎胎侧圆周面上确定至少4 个等间隔点,逐点进行试验。
d. 脱圈压块以规定的下降速度,向胎侧外表面施加压力,直到轮胎与轮辋脱开或达到下表规定的最小脱圈阻力值时为止。记录脱圈时或停止试验时的阻力值。
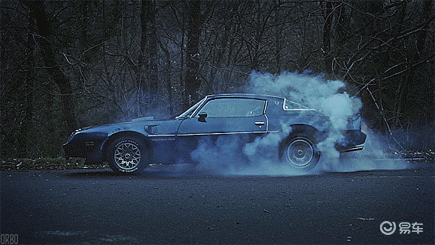
06、高速性能(转鼓法)
轮胎安装在符合规定的标准轮辋上,按下表中规定的气压充气;试验室温度应保持在38℃±3℃。按GB/T7034(ISO10191:1993)进行试验后,轮胎气压不应低于规定的初始气压;轮胎外观检查不应有(胎面、胎侧、帘布层、气密层、带束层、胎圈)脱层,帘布层裂缝、帘线剥离、帘线断裂、崩花、接头裂开、龟裂等缺陷。
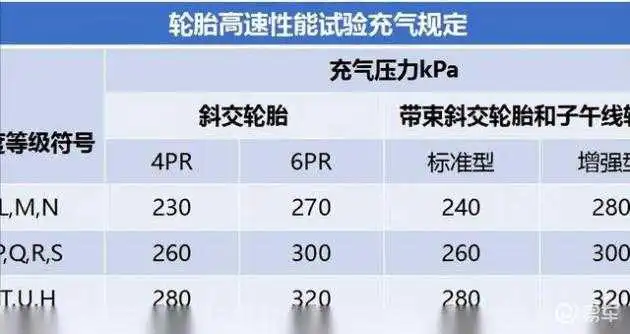
具体试验如下:
a. 将轮胎轮辋组合体在38C士3℃的温度下至少停放3h。
b. 转鼓以匀加速启动到初始试验速度的时间应在10min以内。
c. 其他试验阶段改变速度到速度稳定,所需时间小于1min。
d. 将停放后的轮胎气压重新调整到规定值,再停放15min后,测量轮胎主要尺寸。
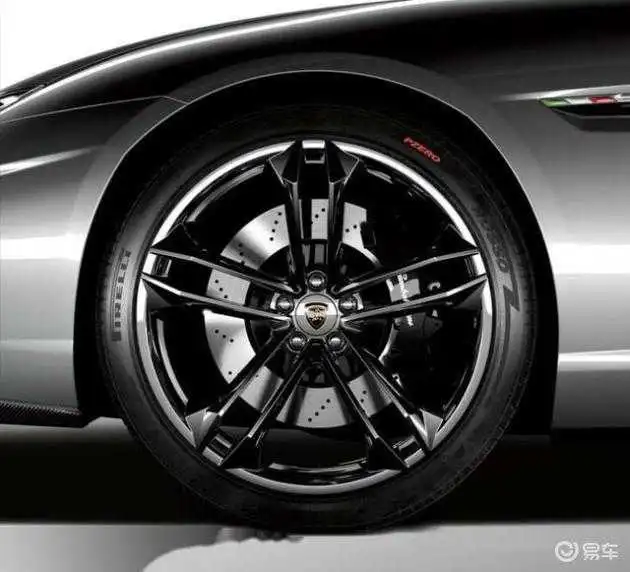
e. 将按上述条件准备好的轮胎轮辋组合体安装在试验轴上,使之垂直转鼓外表面加压,并按规定条件进行试验。
f. 试验按规定程序连续进行,其间不得中断,不得重新调整气压,试验负荷必须保持不变。
g. 轮胎按规定程序完成试验后,要立即停机测量轮胎的气压和主要尺寸,待自然冷却1h后,放掉气压,卸下轮胎进行外观检查。
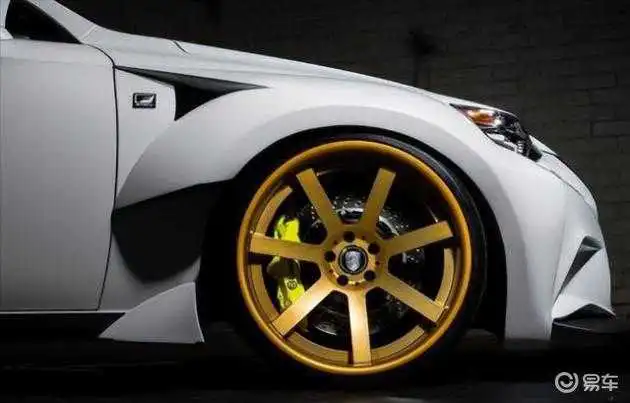
07、耐久性能(转鼓法检查轮胎高负荷连续运行能力)
轮胎安装在符合规定的标准轮辋上,充以下表中规定的气压,将轮胎轮辋组合体在38℃士3℃的温度下至少停放3h。轮胎按GB/T4502(ISO10191:1993)规定的试验条件和试验方法进行耐久性试验后,轮胎气压不应低于规定的初始气压,轮胎外观检查不应有(胎面、胎侧、帘布层等)脱层、帘布层裂缝、帘线剥离、泵花、接头裂开、龟裂等缺陷。具体试验类似上述高速性能测试。
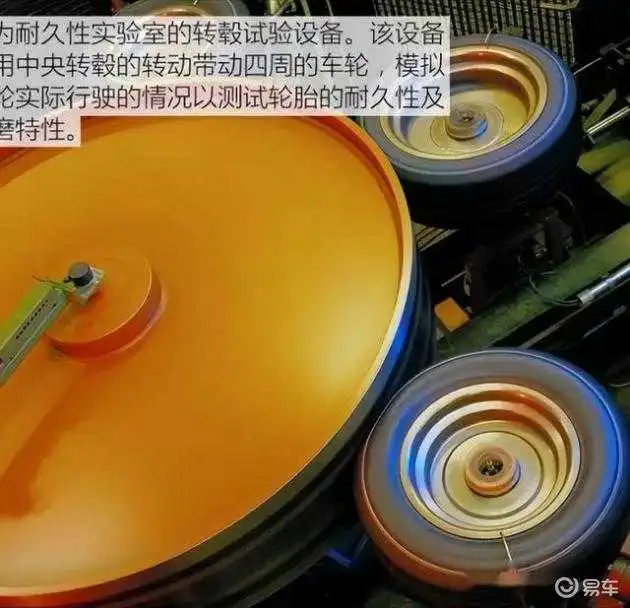
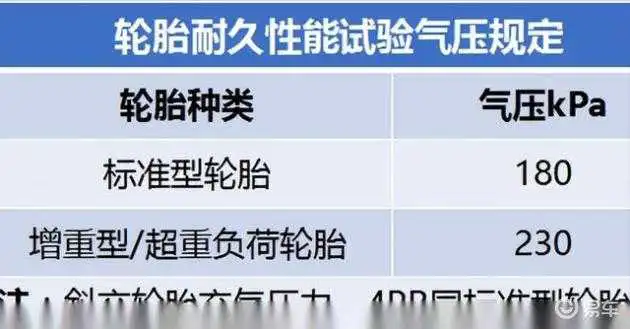
08、车轮整车匹配试验
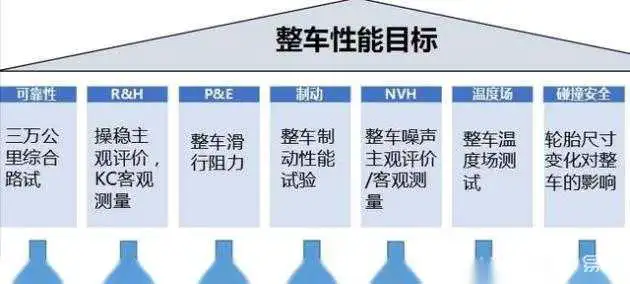
你还知道哪些汽车车轮的相关的知识,欢迎在评论区留言,我是汽车设计工匠,我们下期再聊。
汽车车轮的设计要求有哪些?在进行汽车车轮设计过程当中,我们需要制作哪些实验?这些实验需要满足哪些要求?所有的这一切都是我们进行车轮设计的核心的关键环节。大家好,我是汽车设计工匠。我们今天接着之前的课程来讲解汽车车轮的相关知识。
01、车轮密封性
将试验用未经过涂装的车轮的气门嘴孔密封,车轮的两侧面用带有密封垫的压板压紧,使其密封,再将整个车轮浸入盛满水的水箱内。试验时,充入的压缩空气压力应≥400kPa,充气达到规定气压后30s内,车轮轮辋任何部位不能有任何气泡逸出。
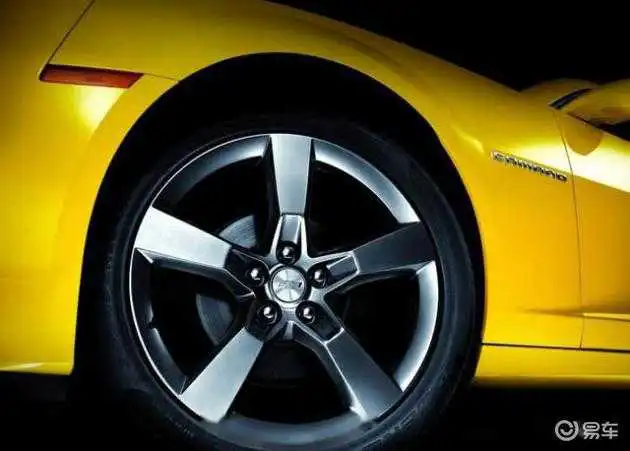
02、车轮的冲击试验
试验环境温度为10℃~38℃,试验设备按GB/T15704-1995中的相应条款规定进行,试验用的轮胎选用整车规定的与之匹配的轮胎,试验方法按GB/T15704中的相应条款规定进行。
试验完后,出现下列情况之一即判定为损坏:轮辐的任一断面处有目测可见的穿透裂纹;轮辐从轮辋上分离;轮胎气压在一分钟内漏尽。
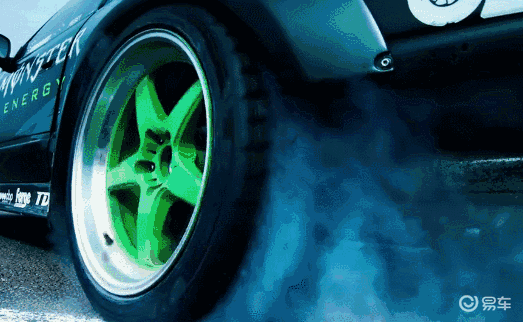
具体试验如下:
a. 轮胎的充气压力必须按车辆制造厂的规定,如无此规定,可按 200kPa充气。
b. 冲头质量为D,确定公式:D=0.6W/180。
式中: D—冲头质量 ±2%;W—最大车轮静载荷,kg
c. 把试验车轮轮胎总成安装在与车辆轮毂一致的连接盘上。车轮安装时,要按车辆或车轮制造厂推荐的方法或用手工拧紧至规定值。
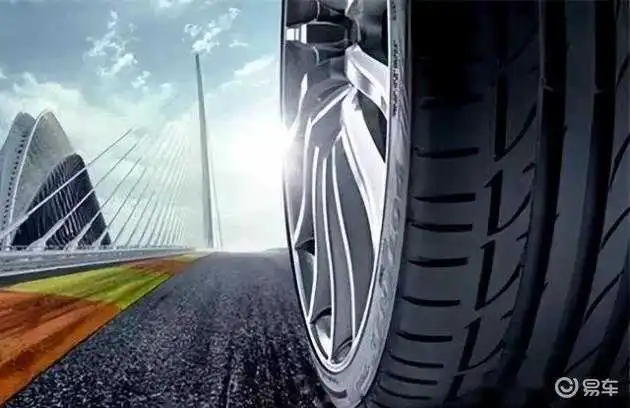
d. 调整冲头下落高度,冲头的下落高度应在轮辋轮缘的最高点上方230±2mm。
e. 调整冲头对车轮的冲击位置,冲头置于轮胎上方,其带有圆角的冲击面刃缘应与轮辋轮缘重叠 25±1mm。
f. 利用试验设备的快速释放机构,让冲头落下,冲击车轮轮胎总成。
03、轮胎尺寸要求
根据整车规定初步选定所需车轮的规格尺寸(主要是轮辋轮辐的参数)和轮胎的规格,此时应综合考虑车轮、轮胎的供应商和GB/T2978《轿车轮胎系列》来设计匹配,选择轮胎时还应考虑到轮胎的负荷指数、侧偏刚度、速度级别以及胎面花纹,以及轮胎的3c认证及美国的DOT认证等。同时,必须考虑所开发或选用的车轮和轮胎之间的匹配性。
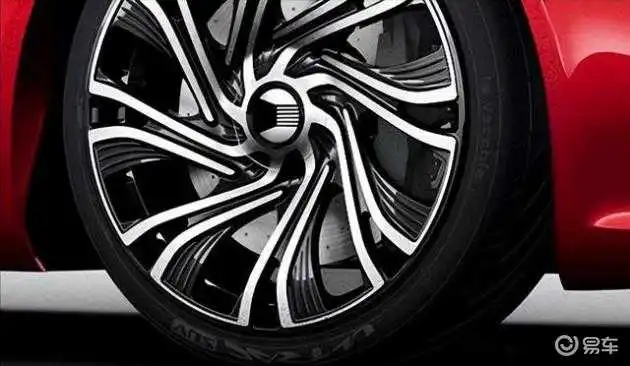
04、轮胎强度
试验室温度应保持在18℃~36℃;其他试验条件、试验方法按照GB/T4053-1996中相应规定执行,试验后轮胎的强度试验破坏能应不低于下表中规定。
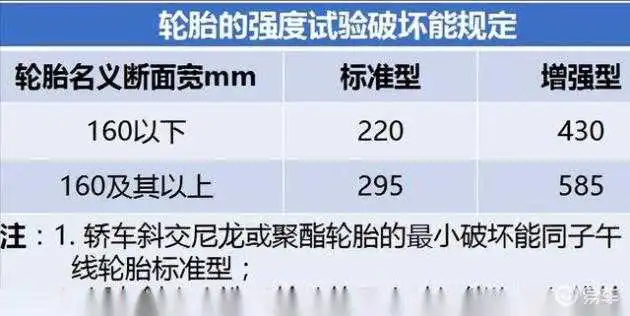
具体试验如下:
a. 将试验轮胎充入规定气压,在试验室温度下至少停放3h后,再重新调到规定气压。
b. 将轮胎固定在试验机上,沿轮胎胎面中心线取大致间隔相等的5个点进行试验。
c. 压头垂直于胎面,并压在靠近胎面圆周中心线的花纹块上,避免压入花纹沟中。
d. 测量每个点的轮胎破坏前瞬时的压力和压入探度(行程),或压头触及轮辆的瞬时压力和行程。在转入下一个点试验前校正气压。

e. 采用自动计算破坏能装置时,当达到规定的最小破坏能后,立即停止压头继续压入轮胎。
f. 如果压头触及轮辋,轮胎未压穿,且未达到最小破坏能值,则此点视为达到最小破坏能。
试验过程中,如果无内胎轮胎无法保持充气压力,允许装入内胎。
g. 计算各点的破坏能:W=F*P/2000。
注:F表示作用力N,P表示行程mm
h. 计算出各点的破坏能的算术平均值,作为该轮胎的破坏能。
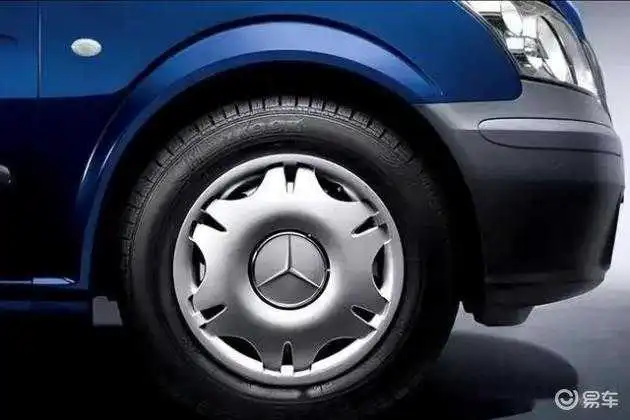
05、脱圈阻力(检查轮胎和轮辋结合紧密程度)
轮胎经GB/T4504(ISO10191:1993)中规定的试验条件和试验方法进行轮胎脱圈阻力试验,每点的脱圈阻力值应不低于下表相应的规定值。
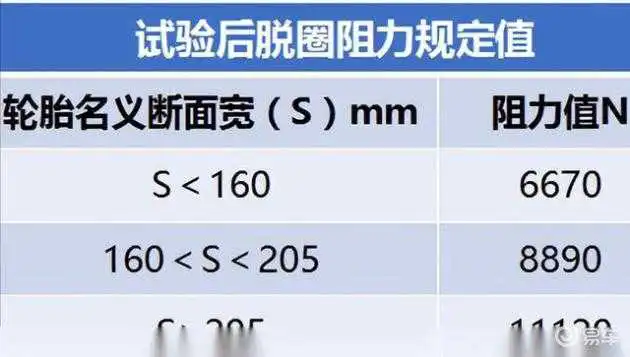
具体试验如下:
a. 将轮胎轮组合体在18℃-36℃的温度下至少停放3h后,再重新调到规定气压。
b. 将轮胎轮辋组合体安装在脱圈阻力试验机上,按规定距离调整脱圈压块的位置。
c. 在轮胎胎侧圆周面上确定至少4 个等间隔点,逐点进行试验。
d. 脱圈压块以规定的下降速度,向胎侧外表面施加压力,直到轮胎与轮辋脱开或达到下表规定的最小脱圈阻力值时为止。记录脱圈时或停止试验时的阻力值。
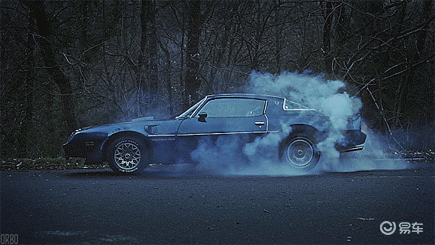
06、高速性能(转鼓法)
轮胎安装在符合规定的标准轮辋上,按下表中规定的气压充气;试验室温度应保持在38℃±3℃。按GB/T7034(ISO10191:1993)进行试验后,轮胎气压不应低于规定的初始气压;轮胎外观检查不应有(胎面、胎侧、帘布层、气密层、带束层、胎圈)脱层,帘布层裂缝、帘线剥离、帘线断裂、崩花、接头裂开、龟裂等缺陷。
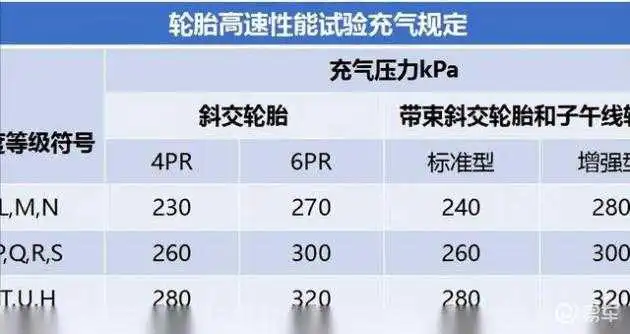
具体试验如下:
a. 将轮胎轮辋组合体在38C士3℃的温度下至少停放3h。
b. 转鼓以匀加速启动到初始试验速度的时间应在10min以内。
c. 其他试验阶段改变速度到速度稳定,所需时间小于1min。
d. 将停放后的轮胎气压重新调整到规定值,再停放15min后,测量轮胎主要尺寸。
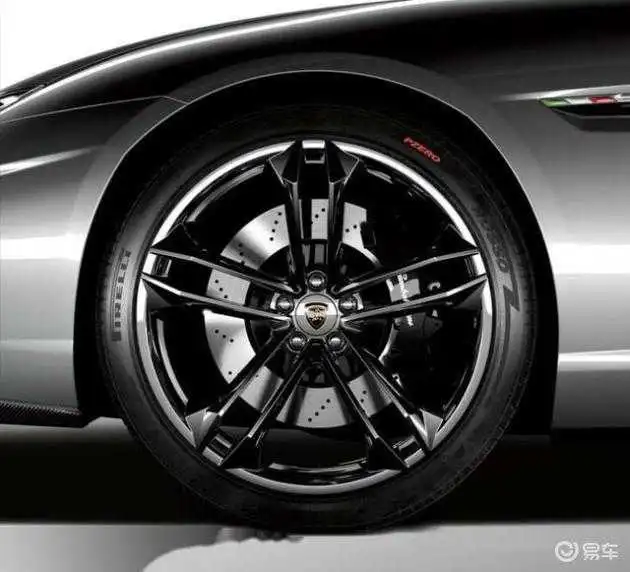
e. 将按上述条件准备好的轮胎轮辋组合体安装在试验轴上,使之垂直转鼓外表面加压,并按规定条件进行试验。
f. 试验按规定程序连续进行,其间不得中断,不得重新调整气压,试验负荷必须保持不变。
g. 轮胎按规定程序完成试验后,要立即停机测量轮胎的气压和主要尺寸,待自然冷却1h后,放掉气压,卸下轮胎进行外观检查。
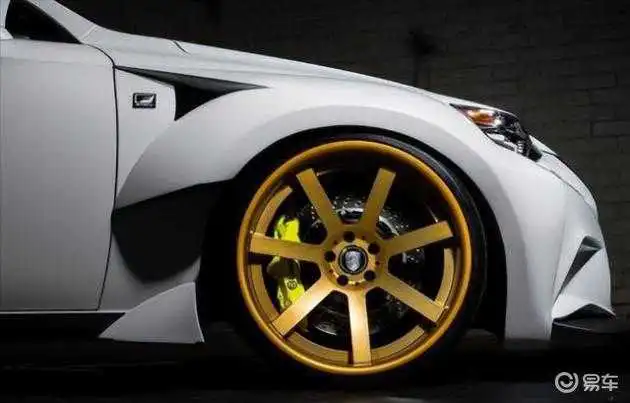
07、耐久性能(转鼓法检查轮胎高负荷连续运行能力)
轮胎安装在符合规定的标准轮辋上,充以下表中规定的气压,将轮胎轮辋组合体在38℃士3℃的温度下至少停放3h。轮胎按GB/T4502(ISO10191:1993)规定的试验条件和试验方法进行耐久性试验后,轮胎气压不应低于规定的初始气压,轮胎外观检查不应有(胎面、胎侧、帘布层等)脱层、帘布层裂缝、帘线剥离、泵花、接头裂开、龟裂等缺陷。具体试验类似上述高速性能测试。
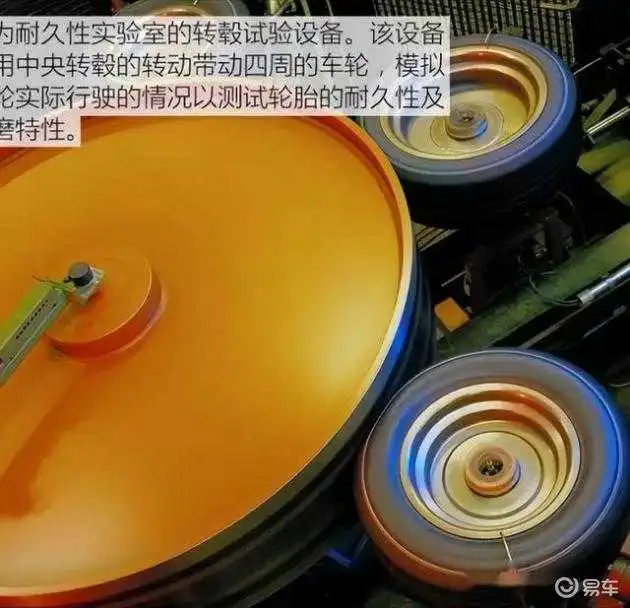
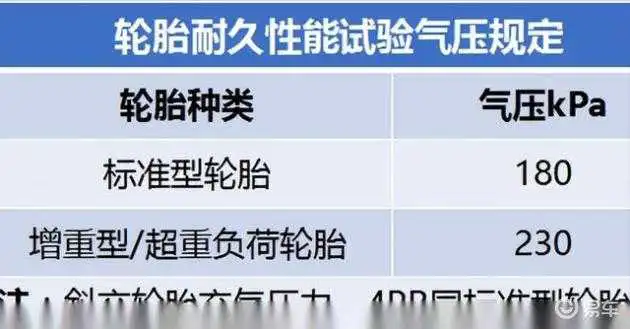
08、车轮整车匹配试验
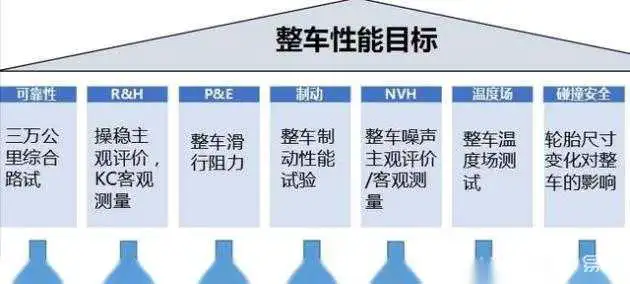
你还知道哪些汽车车轮的相关的知识,欢迎在评论区留言,我是汽车设计工匠,我们下期再聊。
汽车车轮的设计要求有哪些?在进行汽车车轮设计过程当中,我们需要制作哪些实验?这些实验需要满足哪些要求?所有的这一切都是我们进行车轮设计的核心的关键环节。大家好,我是汽车设计工匠。我们今天接着之前的课程来讲解汽车车轮的相关知识。
01、车轮密封性
将试验用未经过涂装的车轮的气门嘴孔密封,车轮的两侧面用带有密封垫的压板压紧,使其密封,再将整个车轮浸入盛满水的水箱内。试验时,充入的压缩空气压力应≥400kPa,充气达到规定气压后30s内,车轮轮辋任何部位不能有任何气泡逸出。
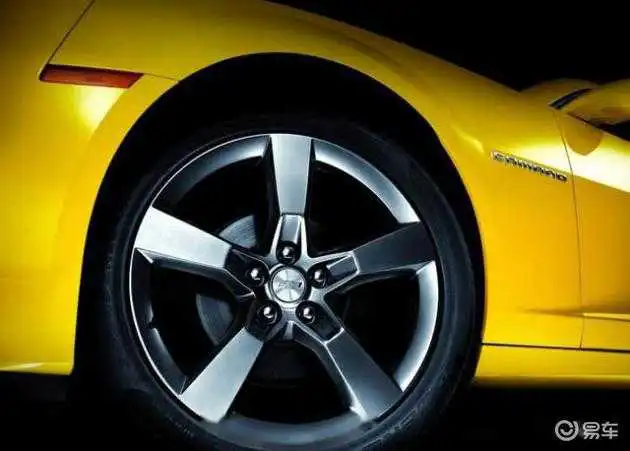
02、车轮的冲击试验
试验环境温度为10℃~38℃,试验设备按GB/T15704-1995中的相应条款规定进行,试验用的轮胎选用整车规定的与之匹配的轮胎,试验方法按GB/T15704中的相应条款规定进行。
试验完后,出现下列情况之一即判定为损坏:轮辐的任一断面处有目测可见的穿透裂纹;轮辐从轮辋上分离;轮胎气压在一分钟内漏尽。
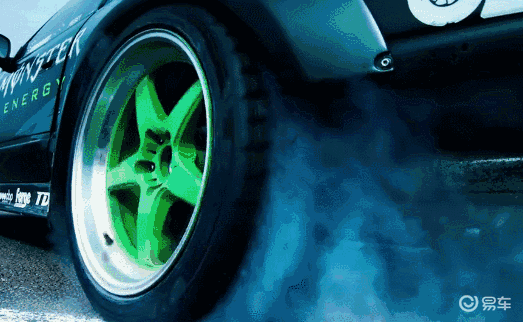
具体试验如下:
a. 轮胎的充气压力必须按车辆制造厂的规定,如无此规定,可按 200kPa充气。
b. 冲头质量为D,确定公式:D=0.6W/180。
式中: D—冲头质量 ±2%;W—最大车轮静载荷,kg
c. 把试验车轮轮胎总成安装在与车辆轮毂一致的连接盘上。车轮安装时,要按车辆或车轮制造厂推荐的方法或用手工拧紧至规定值。
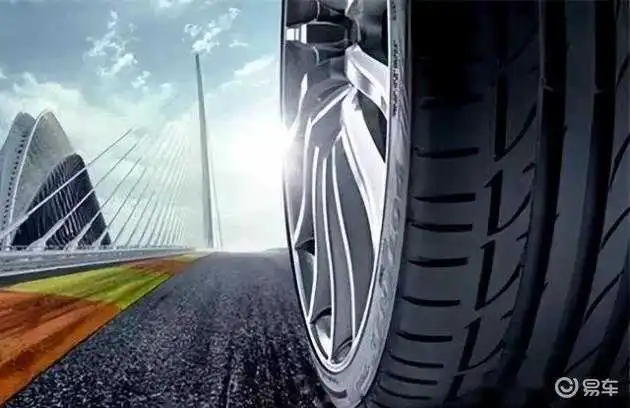
d. 调整冲头下落高度,冲头的下落高度应在轮辋轮缘的最高点上方230±2mm。
e. 调整冲头对车轮的冲击位置,冲头置于轮胎上方,其带有圆角的冲击面刃缘应与轮辋轮缘重叠 25±1mm。
f. 利用试验设备的快速释放机构,让冲头落下,冲击车轮轮胎总成。
03、轮胎尺寸要求
根据整车规定初步选定所需车轮的规格尺寸(主要是轮辋轮辐的参数)和轮胎的规格,此时应综合考虑车轮、轮胎的供应商和GB/T2978《轿车轮胎系列》来设计匹配,选择轮胎时还应考虑到轮胎的负荷指数、侧偏刚度、速度级别以及胎面花纹,以及轮胎的3c认证及美国的DOT认证等。同时,必须考虑所开发或选用的车轮和轮胎之间的匹配性。
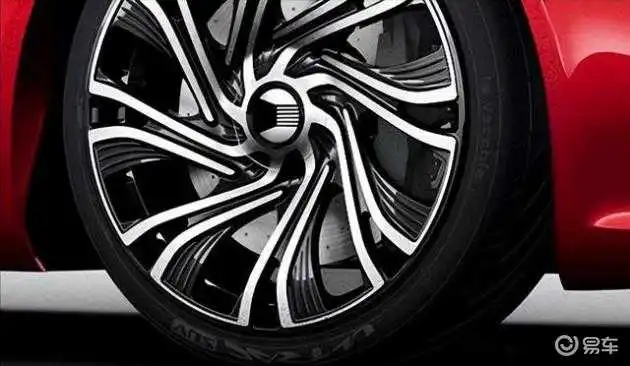
04、轮胎强度
试验室温度应保持在18℃~36℃;其他试验条件、试验方法按照GB/T4053-1996中相应规定执行,试验后轮胎的强度试验破坏能应不低于下表中规定。
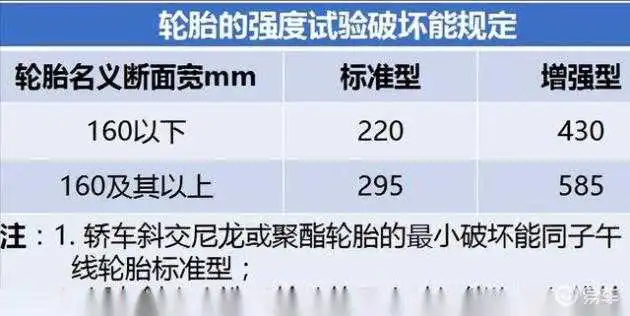
具体试验如下:
a. 将试验轮胎充入规定气压,在试验室温度下至少停放3h后,再重新调到规定气压。
b. 将轮胎固定在试验机上,沿轮胎胎面中心线取大致间隔相等的5个点进行试验。
c. 压头垂直于胎面,并压在靠近胎面圆周中心线的花纹块上,避免压入花纹沟中。
d. 测量每个点的轮胎破坏前瞬时的压力和压入探度(行程),或压头触及轮辆的瞬时压力和行程。在转入下一个点试验前校正气压。

e. 采用自动计算破坏能装置时,当达到规定的最小破坏能后,立即停止压头继续压入轮胎。
f. 如果压头触及轮辋,轮胎未压穿,且未达到最小破坏能值,则此点视为达到最小破坏能。
试验过程中,如果无内胎轮胎无法保持充气压力,允许装入内胎。
g. 计算各点的破坏能:W=F*P/2000。
注:F表示作用力N,P表示行程mm
h. 计算出各点的破坏能的算术平均值,作为该轮胎的破坏能。
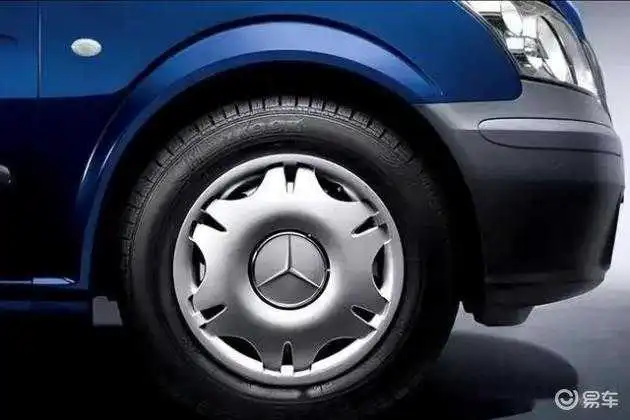
05、脱圈阻力(检查轮胎和轮辋结合紧密程度)
轮胎经GB/T4504(ISO10191:1993)中规定的试验条件和试验方法进行轮胎脱圈阻力试验,每点的脱圈阻力值应不低于下表相应的规定值。
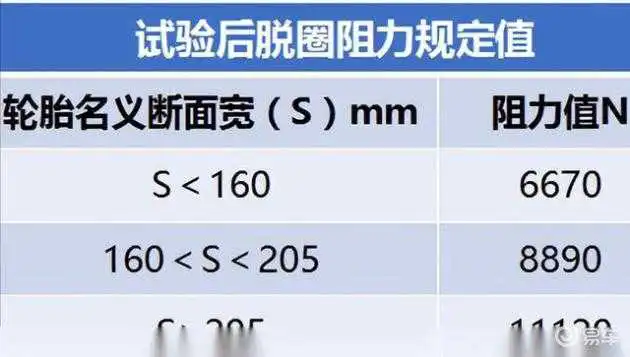
具体试验如下:
a. 将轮胎轮组合体在18℃-36℃的温度下至少停放3h后,再重新调到规定气压。
b. 将轮胎轮辋组合体安装在脱圈阻力试验机上,按规定距离调整脱圈压块的位置。
c. 在轮胎胎侧圆周面上确定至少4 个等间隔点,逐点进行试验。
d. 脱圈压块以规定的下降速度,向胎侧外表面施加压力,直到轮胎与轮辋脱开或达到下表规定的最小脱圈阻力值时为止。记录脱圈时或停止试验时的阻力值。
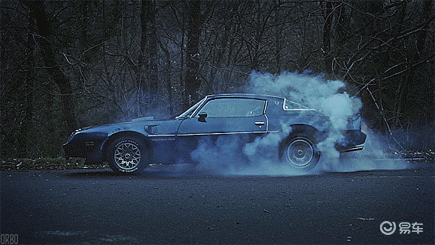
06、高速性能(转鼓法)
轮胎安装在符合规定的标准轮辋上,按下表中规定的气压充气;试验室温度应保持在38℃±3℃。按GB/T7034(ISO10191:1993)进行试验后,轮胎气压不应低于规定的初始气压;轮胎外观检查不应有(胎面、胎侧、帘布层、气密层、带束层、胎圈)脱层,帘布层裂缝、帘线剥离、帘线断裂、崩花、接头裂开、龟裂等缺陷。
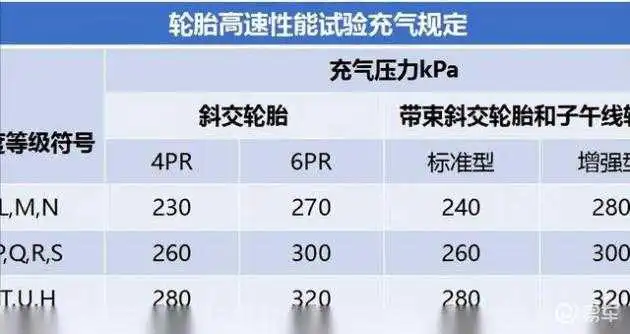
具体试验如下:
a. 将轮胎轮辋组合体在38C士3℃的温度下至少停放3h。
b. 转鼓以匀加速启动到初始试验速度的时间应在10min以内。
c. 其他试验阶段改变速度到速度稳定,所需时间小于1min。
d. 将停放后的轮胎气压重新调整到规定值,再停放15min后,测量轮胎主要尺寸。
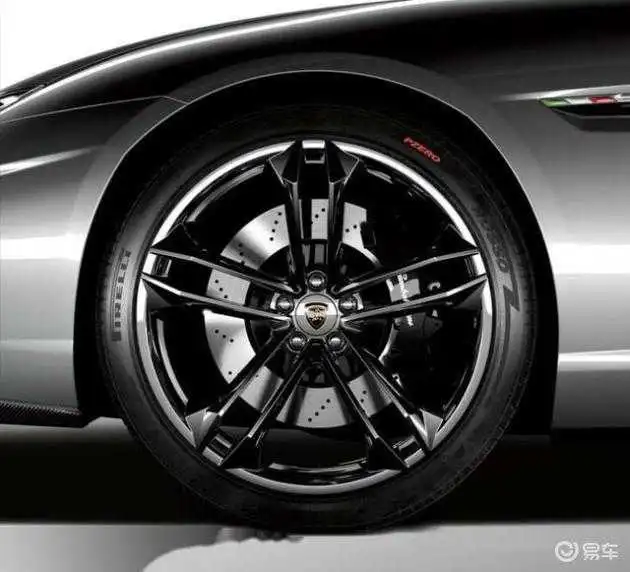
e. 将按上述条件准备好的轮胎轮辋组合体安装在试验轴上,使之垂直转鼓外表面加压,并按规定条件进行试验。
f. 试验按规定程序连续进行,其间不得中断,不得重新调整气压,试验负荷必须保持不变。
g. 轮胎按规定程序完成试验后,要立即停机测量轮胎的气压和主要尺寸,待自然冷却1h后,放掉气压,卸下轮胎进行外观检查。
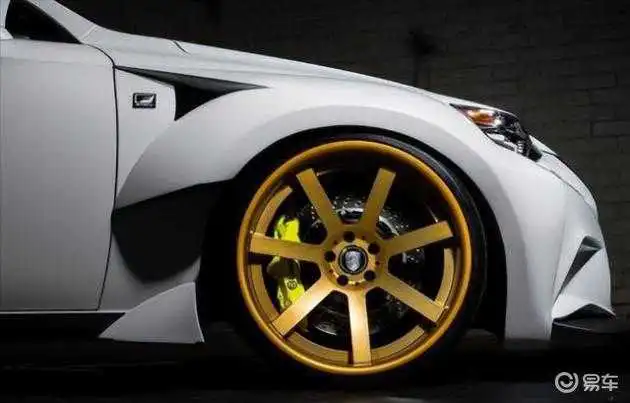
07、耐久性能(转鼓法检查轮胎高负荷连续运行能力)
轮胎安装在符合规定的标准轮辋上,充以下表中规定的气压,将轮胎轮辋组合体在38℃士3℃的温度下至少停放3h。轮胎按GB/T4502(ISO10191:1993)规定的试验条件和试验方法进行耐久性试验后,轮胎气压不应低于规定的初始气压,轮胎外观检查不应有(胎面、胎侧、帘布层等)脱层、帘布层裂缝、帘线剥离、泵花、接头裂开、龟裂等缺陷。具体试验类似上述高速性能测试。
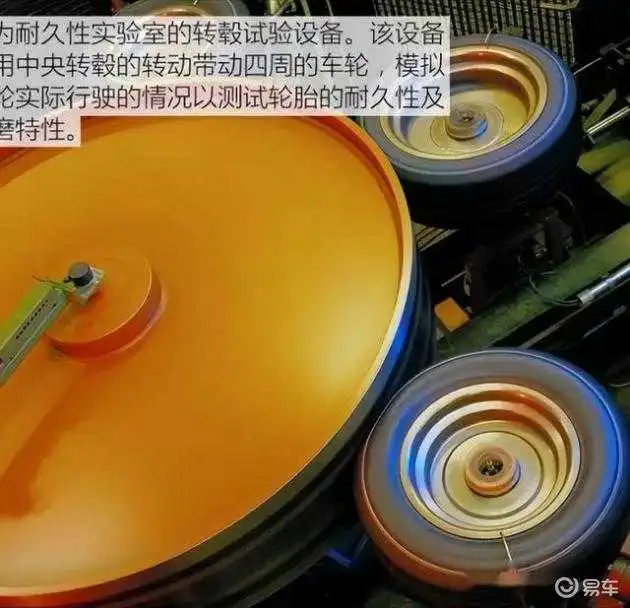
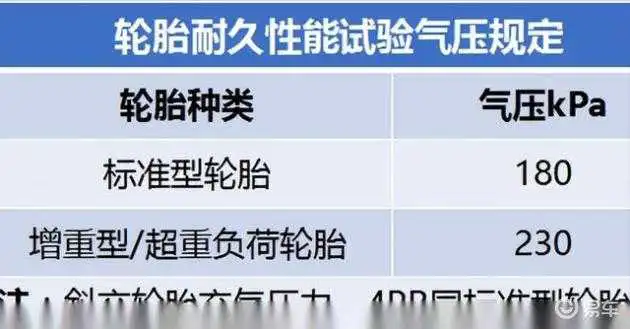
08、车轮整车匹配试验
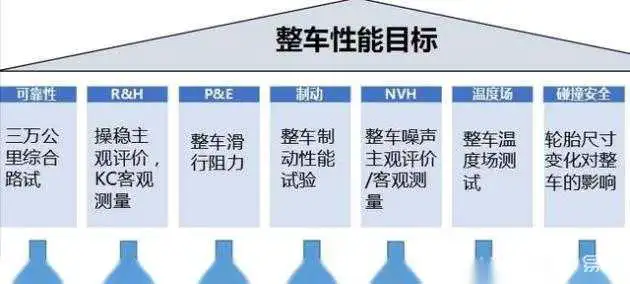
你还知道哪些汽车车轮的相关的知识,欢迎在评论区留言,我是汽车设计工匠,我们下期再聊。
到此这篇dv试验和pv试验(汽车dv试验和pv试验)的文章就介绍到这了,更多相关内容请继续浏览下面的相关推荐文章,希望大家都能在编程的领域有一番成就!版权声明:
本文来自互联网用户投稿,该文观点仅代表作者本人,不代表本站立场。本站仅提供信息存储空间服务,不拥有所有权,不承担相关法律责任。
如若内容造成侵权、违法违规、事实不符,请将相关资料发送至xkadmin@xkablog.com进行投诉反馈,一经查实,立即处理!
转载请注明出处,原文链接:https://www.xkablog.com/bcyy/14026.html